بريد إلكتروني: [email protected]
The Introduction of Common Mineral Processing Methods: Innovations in Crushing and Grinding
In an era where every ton of ore counts, mineral processing has emerged as the linewire between resource scarcity and industrial progress—transforming rocks buried deep within the Earth into the building blocks of smartphones, electric vehicles, and solar panels. At the heart of the common mineral processing methods lie crushing and grinding systems, no longer just brute-force machinery but intelligent ecosystems blending robotics, material science, and circular design. Take South Africa’s Sibanye-Stillwater, where AI-powered jaw crushers now “learn” ore hardness variations in real-time, adjusting gap settings to slash energy use by 22% while maximizing platinum group metal recovery.
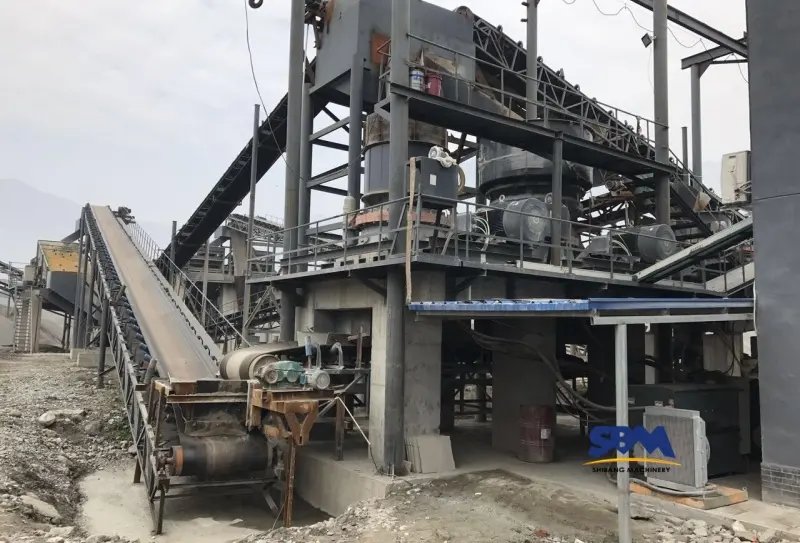
Why Crushing and Grinding Matter in Mineral Processing
Ore crushing and grinding (collectively known as the pulverization process) lays the foundation for subsequent sorting by reducing the particle size of raw materials. This link accounts for 70% of mining energy consumption – this data forces the industry to list equipment optimization and process innovation as a continuous focus for reducing costs and increasing efficiency. Let’s explore the methodologies and breakthroughs shaping these stages.
1. Crushing Techniques: From Traditional to Advanced
Crushing involves breaking large ore fragments into smaller particles using mechanical force. Common mineral processing methods prioritize energy efficiency and reduced environmental impact.
Jaw Crushers and Cone Crushers
While classic jaw crushers continue to dominate primary processing stages with their straightforward mechanics and proven durability, modern كسارات مخروطية have emerged as the preferred solution for tougher secondary operations – particularly when breaking down abrasive materials like quartz-rich granite formations.
2. Grinding Technologies: Precision and Sustainability
Grinding further reduces crushed ore into fine particles, enabling mineral liberation. Advances here focus on lowering energy use and carbon footprints.
Ball Mills and Vertical Roller Mills
Ball mills dominate grinding circuits, using steel balls to pulverize ore. طواحن الأسطوانة الرأسية (VRMs), لكن, offer 20–30% higher energy efficiency by leveraging centrifugal force.
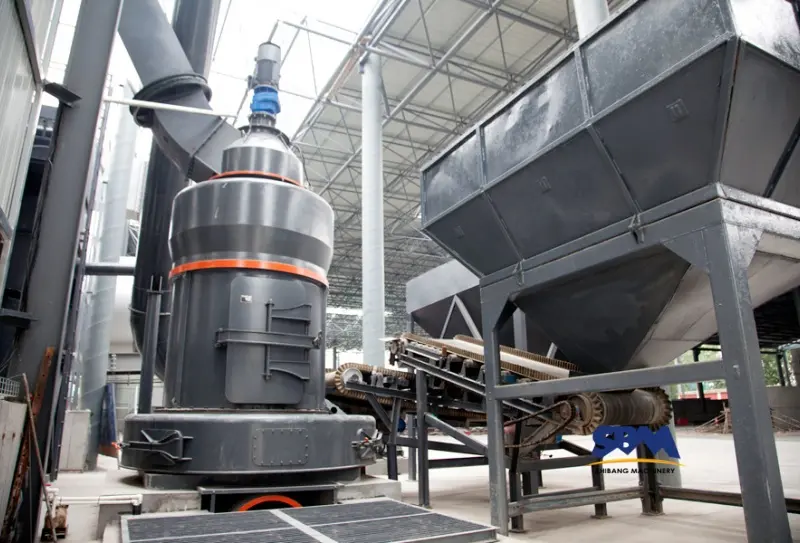
3. Integrated Approaches: Combining Crushing and Grinding
Modern plants often integrate crushing and grinding into hybrid workflows to optimize resource recovery.
Sublevel Caving and Comminution
في السويد, mines like Kiruna employ sublevel caving alongside advanced grinding. This method involves collapsing ore sections into pre-drilled drawpoints, streamlining the transition from crushing to grinding while minimizing waste.
4. Sustainability Trends in Mineral Processing
The push for greener practices has reshaped comminution. Key trends include:
Renewable Energy Integration: Andromeda Metals leverages South Australia’s 70% renewable grid to further cut HPA production emissions.
Dry Processing: Reducing water use in grinding circuits, as seen in Chile’s copper mines, lowers environmental impact.
5. Global Applications and Future Outlook
From Australia’s kaolin-based HPA to MIT’s rare earth advancements, global case studies underscore the versatility of common mineral processing methods. Future innovations may focus on:
AI-Driven Optimization: Machine learning for real-time adjustment of crusher and mill parameters.
Nano-Grinding: Ultra-fine particle production for high-tech applications like lithium-ion batteries.
This article systematically discusses the core position of crushing and grinding technology in mineral processing and its innovation trends. Traditional equipment such as كسارات الفك and ball mills are still widely used, but new technologies such as vertical roller mills achieve a 20-30% increase in energy efficiency through centrifugal force drive, showing significant progress. Global cases show that from Australia’s high-purity alumina production to Chile’s copper mine water-saving solutions, technological innovation is driving resource recovery optimization and reducing environmental impact. In the future, artificial intelligence real-time control and nano-level ultrafine grinding technology may become a breakthrough direction, providing key material support for high-tech fields such as lithium batteries, marking the deep evolution of common mineral processing methods towards intelligent, refined and carbon neutral goals.
المكتب الرئيسي
واتس اب:+8615225176731
بريد إلكتروني: [email protected]
عنوان: لا. 1688, طريق جاوك الشرقي, حي بودونغ الجديد, شنغهاي, الصين.
موقع إلكتروني: https://www.mill-sbm.com/