Имэйл: [email protected]
Төмрийн хүдэр
Main Contents
Imagine no steel. No tall buildings, no bridges, no cargo ships, no working factories – the modern world stops. It all begins underground with a simple-looking rock: төмрийн хүдэр. This isn’t “just a mineral”; it’s the heart of industry. Working directly with the machines that release its value gives you deep respect for iron ore’s path. From seeing its special iron ore color in rough fields, to hearing a crusher break big rocks into smaller pieces – it’s a tough, detailed process. Whether you’re exploring how to find iron ore, working in iron ore mining, or wondering what iron ore is used for, this guide explains clearly. We’ll cover the 4 types of iron ore, show the best place for iron ore worldwide, and explain why the right crushing tech is vital. Let’s dig in!
What Exactly is Iron Ore? Busting the Rock Myth
Okay, the basic definition: төмрийн хүдэр is rock or dirt with enough iron minerals to make mining it worthwhile. But in reality? It’s complicated. It’s never pure iron. You have valuable minerals like hematite эсвэл magnetite mixed with worthless waste rock – quartz, clay, and more. The key? Iron content. While iron exists everywhere in the ground, we only call it “хүдэр” when it’s concentrated enough (usually 20% to as high as 70% iron) to make the huge effort of digging it up pay off. The minerals present are your guide – they decide the iron ore color you see, if a magnet attracts it, and most importantly, how you turn it into something useful.
That first tough step? Бутлах. Hard rock like this needs powerful machines. I’ve seen weaker crushers fail under the constant wear from quartz-heavy Banded Iron rocks. That’s why strong designs, шиг river pebble crushers from SBM БНБ – made to handle tough, abrasive material easily – are essential partners at many mines. Тэгээд what is iron ore used for? Almost all of it goes to make steel – the framework for everything we build and use. Blast furnaces need it. That’s what powers this entire massive industry.
The Rainbow Beneath Our Feet: Iron Ore Color – Your Field Guide
Forget fancy labs for a first glance. Theiron ore color is your prospector’s first clue, screaming the mineral’s identity. It’s not just pretty; it’s practical intel on quality and how much work lies ahead:
- Deep Red to Rusty Brown: You’ve likely found Гематит (Fe₂O₃). This is the workhorse, the most common and economically crucial төмрийн хүдэр globally. That rusty red iron ore color? Blame oxidized iron – nature’s own rust job. Think of the vast, Martian-red landscapes of Australia’s Pilbara – pure hematite country. Get ready for hard, dense rock.
- Jet Black to Dark Gray: Say hello to Магнетит (Fe₃O₄). Its party trick? Strong magnetism. That dense, black iron ore color is a dead giveaway. It often packs a higher iron punch than hematite in theory, but liberating it from its rock prison can be energy-intensive. Finding this feels like striking gold (well, iron-gold) to an exploration geologist.
- Yellowish-Brown to Dull Brown: Likely looking at Лимонит эсвэл “bog iron ore” (FeO(OH)·nH₂O). This iron ore color shouts “weathering!” – it’s hydrated and usually found lounging near the surface. Iron content? Modest. Historically important (think colonial America), but less of a global player today.
- Steely Gray to Dark Reddish-Brown: Could be Siderite (FeCO₃). Its iron ore color is less flamboyant, often a bit nondescript. It’s an iron carbonate, meaning lower iron content and a mandatory roasting step (calcination) before smelting – extra cost, extra hassle. Not the preferred guest at the smelter party.
Table 1: Iron Ore Types – The Color, The Grit, The Reality
Ore Type | Looks Like… (Iron Ore Color) | Avg. Fe Punch | Key Personality Traits | Where You’ll Find It | The Processing Grind |
---|---|---|---|---|---|
Гематит | Deep Red, Rusty Warrior | 50-70% | Tough, Dense, Ignores Magnets | Giant BIFs, Sedimentary Layers | Crush hard, grind, separate (gravity/flotation is key) |
Магнетит | Jet Black Magnetic Marvel | 60-72% | Sticks to Magnets!, Very Dense | BIFs, Igneous Intrusions | Crush hard, grind fine, magnetic separation shines |
Лимонит | Yellow-Brown Weathered One | 35-50% | Soft-ish, Hydrated, Near Surface | Gossans, Old Surface Deposits | Dry it, roast it (calcine), then smelt |
Siderite | Gray/Brown Carbonate | 30-40% | Fizzes in Acid, Lower Grade | Sedimentary Beds, Veins | Must roast it first (drive off CO₂), then smelt |
Learning theseiron ore color signatures is fundamental fieldwork. Spotting that tell-tale red or feeling the pull of black sand with your pocket magnet? That’s the thrill of knowinghow to find iron ore.
Striking Paydirt: How to Find Iron Ore – The Explorer’s Playbook
Want to knowhow to find iron ore? It’s not panning for gold. It’s a high-stakes blend of old-school geology, cutting-edge tech, and gut instinct honed by muddy boots. Here’s the field manual:
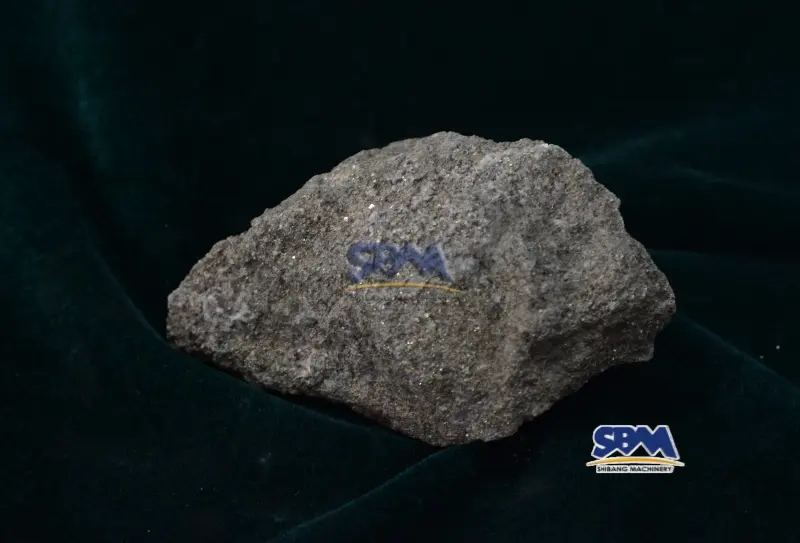
1. Geology is Gospel
Start with the map, always. Төмрийн хүдэр loves specific neighborhoods:
- Banded Iron Formations (BIFs): Ancient (we’re talking billions of years), layered rocks holding the motherlode of high-grade hematite болон magnetite. Target the ancient cores of continents – think Canadian Shield, Aussie Pilbara craton, Brazilian cratons. Spotting the distinctive banding and iron ore color is step one.
- Magmatic Hideouts: Магнетит crystallizes straight from cooling magma. Look for big, deep-seated intrusive bodies – the kind that form mountain roots.
- Sedimentary Basins: Home to oolitic hematite (tiny round grains) болон siderite layers. Find the right ancient sea basin.
- Rusty Clues (Supergene): Weathering near the surface can concentrate iron. It transforms lower-grade BIF into rich hematite “caps” or forms limonite gossans – those rusty, iron-stained outcrops. Seeing that vivid iron ore color staining a hillside? That’s nature’s neon sign screaming “Look here!” – a prospector’s classic how to find iron ore moment.
2. Eyes in the Sky & Tech on the Ground
- Satellite & Drones: Zoom out. Map large-scale rock types, structures, and subtle shifts in vegetation or iron ore color that hint at buried treasure.
- Magnetic Surveys: The go-to for magnetite. Fly a magnetometer over the land or walk it on the ground. That strong magnetic pull? Like a homing beacon for black ore. Makes magnetite deposits relatively “easier” to locate.
- Gravity Surveys: Sense the heft. Massive hematite эсвэл magnetite bodies are dense. Gravity meters detect this extra weight, pinpointing targets.
3. Follow the Geochemical Trail
Collect soil, rock chips, stream sediments. Lab analysis hunts for elevated iron levels and associated elements. It’s detective work, finding anomalies that whisper, “Dig deeper here.”
4. Get Muddy: Real Fieldwork
Technology helps, but nothing beats being on the ground. Geologists walk across the land, carefully examining rock formations, loose stones, and soil. They carry hammers, magnifying glasses, and most importantly, a pocket magnet. Noticing the iron ore color, testing the rock’s weight, seeing striped patterns, feeling the pull of magnetite with a magnet, or spotting rusty surface stains – this is the real skill of finding ore. Discovering loose rocks with the right color and weight can lead directly back to the main ore deposit.
5. Drilling: The Moment of Truth
All the mapping, aerial surveys, and fieldwork lead to this final step. Diamond core drilling or RC drilling digs into the ground. This costs a lot, but it’s the only sure way to answer critical questions: Is iron ore actually present? How deep is it? How good is the quality (grade)? Юу вэ types of iron ore exist there? The drilled samples don’t lie – they reveal whether you’ve found a worthwhile ore body or just scientifically interesting rocks.
From Rock to Ready: Iron Ore Mining – Moving Mountains
Found a viable deposit? Now the real muscle work begins: iron ore mining. Extraction is a colossal engineering feat, dictated by the deposit’s personality – size, хэлбэр, depth, grade, and the surrounding rock.
1. Open-Pit Mining (King of Scale)
Dominates the scene for vast, near-surface deposits, especially those BIF giants.
- The Gig: Imagine sculpting a mountain into a terraced pit. Massive shovels (some scooping 100+ tons per bite) and haul trucks the size of houses strip away overburden (waste rock). Exposed ore gets drilled, blasted into manageable chunks, and hauled away. The scale is mind-boggling – Pilbara mines move more earth daily than some small countries.
- Why it Rules: High-volume, lower cost per ton (compared to underground), relatively safer. Perfect for large, shallow, tabular deposits. You үзнэ үү нь iron ore color layers exposed in the pit walls.
2. Underground Mining (When the Ore Goes Deep)
Used when the prize is buried too far down, steeply dipping, or surface mining is off-limits (under a town, protected area).
- How it’s Done: It’s complex and capital-intensive. Common methods:
- Block Caving: Undercut a massive ore block and let gravity do the heavy lifting as it collapses. Ore is drawn from tunnels below. Used for deep, massive orebodies.
- Sub-level Caving: Similar idea, but breaking the ore into smaller, managed blocks within defined levels.
- Room and Pillar: Carve out “rooms” of ore, leaving sturdy “тулгуур багана” to hold up the roof. Common for flatter-lying deposits closer to surface.
- The Reality: Expensive. Requires sinking shafts, driving kilometers of tunnels, complex ventilation, and rigorous safety protocols. It’s a different world down there.
3. Beneficiation: Where the Magic (and Machinery) Happens
Freshly mined ore (Run-of-Mine or ROM) is usually not blast furnace ready. It’s a mixed bag of valuable iron and worthless gangue, often at lower grades than needed. Beneficiation is the upgrade path:
- Бутлах & Screening: The Gatekeepers: ROM ore is big and chunky. This is where the heavy metal meets the road. Primary crushers (think giant jaw crushers or rugged gyratories) deliver the first, powerful bite. Secondary and tertiary crushers (үргэлж конусан бутлуур or high-pressure grind rolls) take it down further. Screens sort the rubble by size. This stage is brutal. The sheer hardness and abrasiveness of төмрийн хүдэр, especially quartz in BIFs, devours poorly built equipment. You need crushers designed for punishment – the kind of ultra-durable, high-throughput river pebble crushers болон цохилтот бутлуур engineered by SBM China. They’re built to handle the constant assault of hard, abrasive rock, minimizing costly downtime. Getting the crushing right sets up everything that follows.
- Grinding: Takes crushed ore down to sand or finer, liberating iron minerals from the clinging gangue. Energy-hungry but essential.
- Separation – Sorting the Wheat from the Chaff:
- Magnetic Separation: The superstar for magnetite. Powerful magnets (drum or roll types) effortlessly yank the magnetic mineral away from the non-magnetic waste. Elegant and efficient.
- Gravity Separation: Uses density differences. Spirals, jigs, or shaking tables let heavier iron minerals sink away from lighter gangue. A workhorse for hematite.
- Flotation: Adds chemistry. Chemicals make specific minerals repel water (hydrophobic) so they stick to air bubbles and float off. Used for trickier ores or finer particles.
- The Payoff: High-grade iron ore concentrate (60-68% Fe for hematite, үргэлж 65-72% for magnetite) ready for the furnace. The leftover waste? Tailings, stored safely in engineered dams. It’s a process of mass reduction – turning mountains of rock into concentrated value.
The Big Four: Meet the Iron Ore Heavyweights
Lots of iron minerals exist, but only fourtypes of iron ore dominate the commercial stage. Knowing these4 types of iron ore is key to understanding the market and the processing grind:
1. Гематит (Fe₂O₃): The Reigning Champion
- The Stakes: The undisputed king of global төмрийн хүдэр эзлэхүүн. Found in epic BIFs and enriched deposits.
- Personality: Deep red iron ore color (powder it, it’s like rust), non-magnetic, tough as nails. Ер нь 50-70% Fe. Pilbara red is its signature.
- Mining Reality: Almost exclusively massive open-pit operations. Австрали, Brazil, India, South Africa are powerhouses.
- Processing Grind: Demands crushing, скрининг, нунтаглах, and separation (gravity is king, flotation helps). Ignores magnets. That hardness? It means crushers and mills take a beating. Efficient, wear-resistant crushing upfront (like SBM’s heavy-duty designs) is critical to keep costs down and throughput up. You feel the energy consumed grinding this stuff.
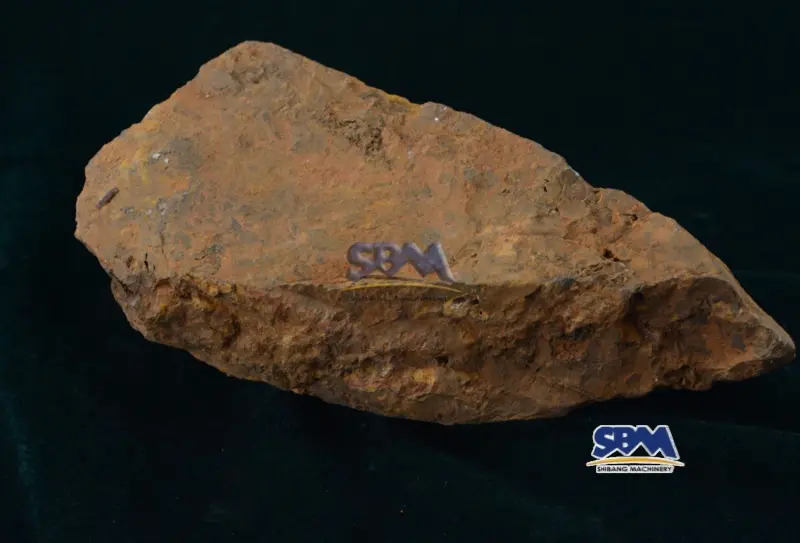
2. Магнетит (Fe₃O₄): The Magnetic Powerhouse
- The Stakes: Valued for its high potential iron content and magnetic personality. Found in BIFs and magmatic deposits.
- Personality: Black/dark gray iron ore color, incredibly dense, болон sticks fiercely to magnets. Theoretical Fe content is tops (72.4%), actual concentrate is superb (often >68% Fe).
- Mining Reality: Open-pit or underground, depending on depth. Австрали, Sweden, Russia, АНУ, Canada have significant plays.
- Processing Grind: Magnetite’s big advantage is magnetic separation – it works very well to pull pure magnetite away from waste rock after crushing and grinding. But magnetite particles are usually very small and tightly stuck, needing heavy grinding to free them. This causes huge energy use during grinding, which is a major cost. The crushing stage still requires handling extremely hard rock. Strong primary crushers that can process large amounts smoothly (like SBM’s specialized equipment) are crucial for feeding those grinding mills cost-effectively. It’s a balance: you get high-quality concentrate, but it demands high energy.
3. Лимонит (Hydrated): The Weathered Relative
- The Stakes: Formed by surface weathering, historically important (“bog iron”), but minor league globally today.
- Personality: Yellowish-brown iron ore color, softer, earthy feel. Iron content is lower (35-50% Fe) and includes water locked in its structure.
- Mining Reality: Usually small-scale, near-surface open pits. More of a historical footnote in Europe/US than a major current player.
- Processing Grind: Needs drying and intense heating (calcination) to drive off the water before хайлуулах. Adds significant cost and complexity. Often used locally if available, rarely worth long-distance haul.
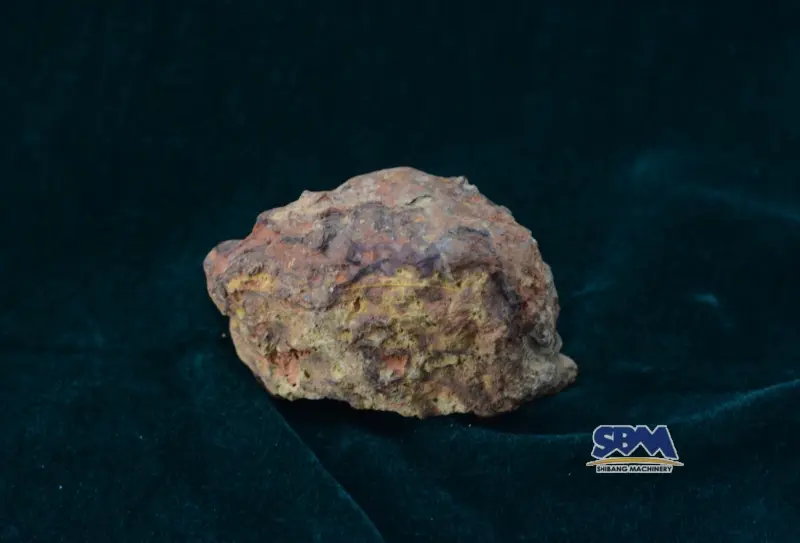
4. Siderite (FeCO₃): The Carbonate Challenge
- The Stakes: An iron carbonate. Historically mined in places like the UK, but economically tricky now.
- Personality: Iron ore color varies (gray, brown, шар), often with a pearly sheen. Lowest Fe content of the main crew (30-40%). Fizzes in acid – a quick field test.
- Mining Reality: Mined from sedimentary layers or veins. Niche player.
- Processing Grind: Must be roasted (calcined) to drive off CO₂ and convert it to iron oxide before хайлуулах. Yet another expensive, energy-intensive pre-step. Often blended with higher-grade ores if used at all. Not the favorite child of smelter operators.
Table 2: The Iron Ore Heavyweights – A Reality Check
Өвөрмөц | Гематит (The King) | Магнетит (The Magnetic Marvel) | Лимонит (The Weathered One) | Siderite (The Carbonate) |
---|---|---|---|---|
Looks Like | Deep Red, Rusty | Jet Black | Yellow-Brown | Gray/Brown |
Fe Content | Solid (50-70%) | Highest Potential (60-72%) | Modest (35-50%) | Lowest (30-40%) |
Magnetism | Ignores Magnets | Loves Magnets! | Weak Attraction | Ignores Magnets |
Processing Key | Crush Hard, Grind, Gravity/Float | Crush Hard, Grind FINE, Mag Sep | Dry, Roast (Calcinate) | Roast (Calcinate), Smelt |
Market Role | #1 (Volume Leader) | #2 (Premium Concentrate) | Minor Player | Minor Player |
Big Headache | Хард рок, Grind Energy | Massive Grind Energy Cost | Low Grade, Water Weight | Low Grade, CO₂ Burden |
Powering the World: What is Iron Ore REALLY Used For?
Understandingwhat iron ore is used for boils down to one word: Steel. Seriously, over 98% of all that mined rock ends up fueling steel production. Үүнийг задалцгаая:
1. Steelmaking: The Behemoth
- Blast Furnace (BF) – The Standard Method: Processed төмрийн хүдэр (as sinter, pellets, or lump ore), coke (baked coal), болон шохойн чулуу enter a blast furnace’s hot chamber. Inside, extreme heat melts all materials. Coke turns iron oxides into liquid metallic iron, while limestone removes impurities by creating slag. This produces molten “pig iron” – high in carbon. The pig iron then moves to a Basic Oxygen Furnace (BOF), where oxygen blows through it to remove extra carbon, making steel. This remains the dominant steelmaking process worldwide.
- Direct Reduced Iron (DRI) – The Gas Route: This process uses natural gas (or coal) to remove oxygen from төмрийн хүдэр pellets or lump ore without melting it. The result is solid “sponge iron” (called DRI or HBI). This cleaner iron material is mostly melted in Electric Arc Furnaces (EAFs), usually mixed with a large amount of recycled scrap steel. It’s a more adaptable approach that can be greener (especially using clean hydrogen) and is becoming increasingly important.
- Steel’s Ubiquity – It’s EVERYWHERE: Look around. Steel made from iron ore forms the backbone of modern life:
- Buildings: Skyscrapers, bridges, steel bars in concrete
- Transportation: Cars, ships, trains, rails
- Machinery: Excavators, turbines, factory equipment
- Energy: Pipelines, power towers, wind turbines
- Гэр: Refrigerators, washing machines, food cans
It’s completely essential.
2. Pig Iron Casting: The Direct Route
A smaller slice of blast furnace pig iron gets cast directly into molds. This “cast iron” is hard and wear-resistant (but brittle). Think engine blocks, manhole covers, pipes, and yes, those vintage skillets.
3. Other Niche Players
- Pigments: Some iron oxides (ochres, umbers), sometimes from ore processing byproducts or specific deposits, color paints, бүрээс, and even cosmetics.
- Heavy Media: Finely ground magnetite (or ferrosilicon) is dense. It’s used as a “heavy medium” in dense media separation plants (like coal washing) to float light stuff and sink heavy stuff based on density.
- Radiation Shielding: Iron’s density makes it useful in concrete for shielding against radiation (Жишээ нь e., around nuclear facilities or medical X-ray rooms).
- Catalysts: Iron compounds play roles in key chemical processes, like the Haber process making ammonia for fertilizer.
Global Iron Giants: Where the Real Ore Action Is
Talking about thebest place for iron ore? Depends if you mean sheer volume, highest quality, or easiest access. Here’s the global landscape from the pit face:
1. Австрали: The Unrivaled Export Juggernaut
- The Goods: Enormous reserves, dominated by high-grade hematite in the iconic Pilbara (WA). Home to mining titans: Rio Tinto, BHP, Fortescue. This is benchmark ore.
- Production Muscle: Consistently world’s #1 exporter, often top producer. Highly efficient mega-mines close to coast = low-cost shipping to Asia. Pilbara operations are engineering marvels.
- Why it’s Top Dog: Sheer scale, consistently high grade, world-class mining/logistics infrastructure, stable operating environment, and prime location feeding the hungry Asian steel mills (Хятад, Япот, Korea). Pilbara ore sets the standard.
2. Brazil: Home of the Purest Giants
- The Goods: Possesses some of the planet’s largest and highest-grade deposits, especially the legendary hematite of the Carajás Mountains (Pará) – Vale’s crown jewel. Exceptionally pure ore (үргэлж +65% Fe).
- Production Muscle: A heavyweight global producer and #2 exporter. Quality commands premium prices.
- The Catch & The Strength: Logistical hurdles exist – hauling ore hundreds of km from mine to Atlantic ports. But the unparalleled quality and scale of Carajás make it indispensable. When the market wants premium lump or pellet feed, Brazil often answers.
3. The Supporting Cast – Major Players
- Хятад: The elephant in the room. World’s #1 steelmaker and төмрийн хүдэр consumer. Also a huge producer itself, but much domestic ore is lower grade, complex, and costly to mine/process. Relies heavily on imports (especially Aussie and Brazilian high-grade). Drives global prices.
- India: Massive reserves, primarily hematite. A significant producer and growing exporter. Faces challenges with ore grade consistency, infrastructure bottlenecks (rail/port), and regulatory shifts. Key supplier, especially to nearby markets.
- Russia: Huge reserves, centered on the Kursk Magnetic Anomaly (magnetite). Major producer, but high domestic steel consumption eats into exports. Current geopolitical realities severely complicate export logistics and market access.
- Өмнөд Африк: Significant high-grade hematite reserves, especially premium lump ore from the Northern Cape (Sishen mine). Key supplier to Europe and Asia. Faces persistent challenges moving ore efficiently via rail to ports.
- Тамирч: Important producer from the Labrador Trough (hematite & magnetite). High-quality ore, critical supplier to North American and European mills. Operates in a challenging climate but delivers reliable quality.
Table 3: Iron Ore Titans – Reserves, Production & Realities (Illustrative)
Country | Heartland | Ore Type Star | Reserves (Gt) | Production (Mt/yr) | Key Strength / Reality Check |
---|---|---|---|---|---|
Австрали | Pilbara (WA) | Гематит | 50+ | 900+ | Scale, High Grade, Export Machine |
Brazil | Carajás (Pará) | Гематит | 30+ | 400+ | Unmatched High Grade Quality |
Хятад | Multiple | Hematite/Mag | 20+ | 800+ (Consumes >!) | Massive Market, Complex Domestic Ore |
India | Odisha, Jharkhand… | Гематит | 7+ | 250+ | Large Reserves, Growing Exporter, Logistical Hurdles |
Russia | Kursk, Siberia | Магнетит | 25+ | 100+ | Large Reserves, Domestic Focus, Geopolitical Constraints |
Өмнөд Африк | Northern Cape | Гематит | 1+ (Hi-Grade) | 70+ | Premium Lump Ore, Rail Challenges |
Тамирч | Labrador Trough | Hematite/Mag | 6+ | 50+ | Reliable Quality, N.A. & EU Supply, Harsh Climate |
The Gritty Chain – From Ore Dust to Opportunity
Standing by our main jaw crusher breaking Pilbara hematite – loud noise, strong shaking, raw power – gives a real sense of scale. That deep red rock, known by its special iron ore color, comes from top sources like Australia’s Pilbara or Brazil’s Carajás. It holds real promise. Finding ore is step one. Mining moves huge amounts of earth. Бутлах – where big rocks hit steel – needs tough, reliable machinery. It’s essential. Watching our SBM БНБ crushers work non-stop in tough mines, taking wear that would break other machines, shows their value. They make production happen. Knowing the 4 ore types – hematite (main), magnetite (magnetic), limonite (weathered), siderite (carbonate) – is practical. It decides technology needs, energy use, costs, болон what iron ore builds: our world’s base.
Iron ore mining deals with constant problems: using up the best ores, pressure to cut environmental damage (especially carbon), and changing markets linked to global steel needs. But the main forces – worldwide growth, growing cities, infrastructure demands – stay strong. The future needs new solutions: better exploration tools, more efficient mining and processing (бутлах зэрэг), and big advances in low-carbon steelmaking (like hydrogen). Continuous improvements to tough, efficient equipment – starting with key primary crushers – are essential. This fast-changing field depends on rock that holds up modern life. That path from seeing iron ore color underground to steel in buildings or cars? It shows human cleverness with Earth’s materials. The hunt for new deposits and better ways continues – hard but crucial work we back, ton by ton.