Correo electrónico: [email protected]
Proses pengolahan bijih besi
Apa proses pengolahan bijih besi? Bayangkan suasana di lokasi tambang pagi itu. Kabut tipis baru saja tersibak, udara dingin menusuk tulang. Di depan kami, bongkahan bijih besi mentah hasil peledakan malam sebelumnya teronggok, besar-besar, keras, dan berdebu. Mereka tampak seperti batu biasa, tak berguna. Tapi bagi kami yang berkecimpung di industri ini, setiap bongkahan itu adalah permulaan sebuah petualangan panjang. Sebuah perjalanan rumit nan menakjubkan untuk mengubah bahan mentah itu menjadi baja yang membangun dunia. Proses pengolahan bijih besi ini bukan cuma urusan mesin dan kimia; ini tentang ketelitian, pengalaman, dan sedikit sentuhan seni. Mari kita telusuri bersama, seperti saya sering jelaskan ke tim di lapangan.

Mengenal “Si Kasar” dari Dalam Bumi: Apa Itu Bijih Besi?
Sebelum kita bahas proses pengolahan bijih besi, kita perlu kenal baik-baik dengan “karakternya”. Bijih besi itu bukan besi murni yang siap pakai. Ia lebih seperti batuan yang menyimpan harta karun besi di dalamnya, bercampur dengan berbagai mineral lain (banda). Jenis-jenis utamanya punya sifat berbeda, dan ini penting banget untuk menentukan strategi pengolahan mineral besi nantinya. Dari pengalaman, salah identifikasi jenis bijih di awal bisa berakibat mahal di tahap selanjutnya!
- Hematit (Fe₂O₃): Si merah kecoklatan ini paling sering kami temui. Kandungan besinya lumayan, sekitar 50-65%. Tampilannya kadang menipu, tapi dia yang paling banyak jadi “bahan baku utama” di banyak pabrik.
- Magnetit (Fe₃O₄): Nah, ini favorit banyak operator! Warnanya hitam legam, dan yang paling khas, dia tertarik magnet. Kandungan besinya bisa nyampe 60-70% bahkan lebih! Efisiensinya biaa lebih tinggi dalam pemisahan. Kalau nemu deposit magnetit bagus, raa kayak ketemu harta karun!
- Goethite/Limonite (FeO(OH)·nH₂O): Bijih besi yang mengandung air ini. Kandungan besinya lebih rendah, dan seringkali lebih “rewel” dalam pengolahan. Tapi tetap penting, apalagi di sumber-sumber tertentu.
- Siderite (FeCO₃): Si karbonat ini. Butuh perlakuan khusus seperti pemanggangan sebelum diolah lebih lanjut. Tidak terlalu umum, tapi tetap perlu diwaspadai.
Memahami karakter masing-masing jenis bijih ini seperti mengenal musuh (atau kawan) sebelum bertempur. Ini fondasi untuk merancangalur produksi bijih besi yang efisien dan minim masalah.
Nivel 1: Persiapan Bijih – “Membongkar” Batu Besar Jadi Kecil
Langkah pertamaproses pengolahan bijih besi ini mungkin terdengar sederhana: memecah bongkahan besar jadi kecil-kecil. Pero no se equivoque, ini krusial! Bayangkan bijih yang baru keluar dari tambang, ukurannya bisa sebesar mobil kecil! Tujuannya jelas: membebaskan butiran-butiran mineral besi yang berharga dari batu samping (banda) yang mengepungnya, sekaligus membuat ukurannya cocok untuk proses pemisahan selanjutnya.
Penghancuran (Aplastante): Ini Bagian Kami!
- Penghancuran Primer: Di sinilah mesin berat seperti Rompe mandíbulas beraksi. Mesin ini ibarat raksasa yang punya rahang besi. Tugasnya? Menerima bongkahan besar dan memecahkannya jadi pecahan berukuran sekitar 150-250 milímetro. Saya ingat betul, dulu di proyek Kalimantan, satu unit Rompe mandíbulas kami (seperti seri PE) harus bekerja ekstra keras menangani bijih yang sangat abrasif. Keandalan di tahap ini menentukan segalanya. Bunyi mesinnya yang berdebum dan getarannya yang terasa sampai ke tulang itu adalah “musik” yang menandakan produksi berjalan. Kalau mesin ini ngambek, seluruh pabrik bisa ikutan berhenti!
- Penghancuran Sekunder & Tersier: Setelah di”gebuk” oleh jaw crusher, material masuk ke tahap penghalusan lebih lanjut dengan Trituradora de cono o trituradora de impacto. Targetnya? Mendapatkan ukuran lebih kecil lagi, biaa di bawah 25mm. Untuk bijih besi yang keras dan abrasif, Trituradora de cono sering jadi pilihan utama karena lebih tahan aus. Pengalaman pahit kami pernah terjadi ketika memaksakan impact crusher untuk bijih magnetit super keras – biaya penggantian part ausnya membengkak! Pemilihan alat yang tepat di sini bukan cuma soal harga mesin, tapi lebih ke biaya operasional jangka panjang. Efisiensi energi juga jauh lebih baik jika alatnya cocok dengan karakter bijih.
Penggilingan (Grinding): Menuju Kehalusan Ekstrim
Kalau crushing sudah membuat bijih “cukup kecil”, grinding membuatnya menjadi sangat halus, bahkan seperti tepung (seringkali lebih kecil dari 0.1mm!). Alat utamanya adalah Ball Mill o Rod Mill. Bayangkan sebuah drum besar berputar, di dalamnya diisi dengan bola-bola baja atau batang baja. Material dimasukkan, dan saat drum berputar, bola-bola itu saling memukul dan menggerus bijih sampai halus. Proses ini sangat boros energi! Tapi ini harga yang harus dibayar untuk membebaskan sebanyak mungkin butiran mineral besi dari ikatannya. Suara gemuruh ball mill yang beroperasi 24/7 itu seperti detak jantung pabrik. Kalau tiba-tiba diam, pasti ada masalah serius.
Tabel: Kebutuhan Ukuran Partikel untuk Metode Pemisahan Berbeda – Pelajaran dari Lapangan
Metode Pemisahan | Ukuran Partikel Ideal | Catatan Praktis & Pengalaman Kami |
---|---|---|
Pemisahan Magnetik | Relatif kasar (1milímetro – 0.15milímetro) | Paling efisien untuk magnetit. Ukuran lebih besar memudahkan pemisahan dan mengurangi risiko kehilangan mineral halus. Kalau terlalu halus, bisa lolos tanpa tertarik! |
Flotasi | Sangat halus (<0.15milímetro, bahkan <0.045milímetro) | Butuh permukaan luas. Semakin halus, semakin bagus untuk “menempel” ke gelembung udara. Tapi hati-hati, bijih yang terlalu halus juga bisa meningkatkan konsumsi reagen kimia dan biaya pengolahan limbah (tailing). |
Pemisahan Gravitasi | Bervariasi (5milímetro – 0.075milímetro) | Tergantung alat (Jig, Spiral, dll). Perbedaan berat jenis (density) harus jelas. Untuk bijih besi, metode ini sering dipakai sebagai tahap awal (pre-concentration) sebelum masuk ke magnetik atau flotasi, terutama kalau ada mineral berat lain yang menguntungkan. |
Nivel 2: Konsentrasi – “Memisahkan Gandum dari Sekam”
Inilah inti dariproses pengolahan bijih besi: memisahkan si mineral besi yang berharga dari material pengotor (banda) yang tidak berguna. Tekniknya beda-beda, tergantung sifat alami bijihnya. Ini bagian yang sering penuh kejutan!
Pemisahan Magnetik (Magnetic Separation): Sangat Efektif untuk Magnetit!
Ini biaa jadi andalan utama kalau bijihnya magnetit. Prinsipnya sederhana tapi canggih: material yang sudah halus dialirkan di atas atau di dekat magnet kuat (bisa magnet permanen atau elektromagnet). Partikel magnetit yang tertarik magnet akan menempel atau dibelokkan jalurnya, terpisah dari gangue yang non-magnetik. Kekuatan magnetnya krusial, biaa di kisaran 5000-6000 gauss atau lebih. Saya selalu terkesima melihat partikel hitam itu tiba-tiba “terbang” ke arah magnet, seperti ada sihir. Efisiensi metode ini tinggi, dan biaya operasinya relatif lebih rendah dibanding flotasi. Tapi ya, hanya efektif untuk mineral yang bersifat magnetik seperti magnetit.
Flotasi (Flotation): Seni Mengapungkan Mineral
Untuk hematit atau bijih yang tidak magnetis, flotasi sering jadi pilihan. Ini proses kimia-fisika yang cukup rumit. Bijih halus dicampur air dan ditambah reagen kimia khusus (kolektor, frother, dll). Reagen kolektor ini membuat permukaan partikel besi menjadi “takut air” (hidrofobik). Lalu, udara ditiupkan ke dalam campuran, menciptakan gelembung-gelembung kecil. Partikel besi yang sudah hidrofobik akan menempel pada gelembung udara dan terangkat ke permukaan membentuk buih. Buih inilah yang kemudian dikeruk sebagai konsentrat. Sementara, partikel pengotor yang “suka air” (hidrofilik) akan tenggelam. Proses ini seperti sulap! Tapi butuh pengawasan ketat. Salah sedikit takaran reagen, atau pH air yang tidak pas, hasilnya bisa kacau. Pengalaman di lapangan mengajarkan, operator flotasi yang berpengalaman itu sangat berharga!
Pemisahan Gravitasi (Gravity Separation): Memanfaatkan Perbedaan Berat
Teknik ini memanfaatkan perbedaan berat jenis (density) antara mineral besi (biaa lebih berat) dan gangue (biaa lebih ringan). Alat seperti Jig o Spiral Concentrator digunakan. Dalam media air, partikel yang lebih berat akan tenggelam lebih cepat atau bergerak ke jalur berbeda dibanding partikel ringan. Ini metode yang relatif lebih sederhana dan biayanya rendah, serta ramah lingkungan karena minim bahan kimia. Sering digunakan sebagai tahap awal untuk mengurangi beban proses selanjutnya (pre-concentration), atau untuk jenis bijih tertentu dimana perbedaan berat jenisnya sangat mencolok. Melihat partikel mineral berat terpisah dengan sendirinya karena gravitasi selalu membuat saya ingat betapa hukum alam itu bekerja dengan elegan.
Hasil dari tahap konsentrasi yang sukses adalah konsentrat bijih besi. Ini bubuk halus yang kandungan besinya jauh lebih tinggi (Poder 60-68% Fe untuk magnetit, o 58-64% untuk hematit) dibanding bijih mentah. Bayangkan, massa material yang harus diangkut dan diolah selanjutnya bisa berkurang drastis karena gangue-nya dibuang! Ini penghematan biaya logistik dan energi yang signifikan dalam proses pengolahan bijih besi.
Nivel 3: Aglomerasi – “Membentuk Kembali si Bubuk Halus”
Konsentrat bijih besi itu berupa bubuk sangat halus. Kalau dimasukkan begitu saja ke dalam blast furnace (tungku tiup), hasilnya bakal berantakan! Bubuk halus itu akan menyumbat aliran gas, reaksinya tidak merata, dan efisiensi turun drastis. Makanya, tahapan pengolahan bijih besi berikutnya adalah mengaglomerasi, alias membentuk kembali bubuk itu menjadi gumpalan yang lebih besar, fuerte, dan berpori.
1. Pembuatan Pelet (Pelletizing): Membuat “Kelereng” Besi
Ini proses yang cukup “estetik”. Konsentrat halus dicampur dengan bahan pengikat (biaa bentonit, sejenis lempung) dan sedikit air. Campuran basah ini kemudian dimasukkan ke dalam alat bernama pelletizing disc (piringan berputar) o pelletizing drum (drum berputar). Gerakan berputar ini membuat campuran menggulung dan membentuk bola-bola kecil seperti kelereng, biaa berdiameter 9-16 milímetro. Pelet basah ini masih rapuh. Entonces, mereka harus dikeringkan dulu, lalu dimasukkan ke dalam tungku bersuhu sangat tinggi (sekitar 1300°C) untuk proses indurasi (pengerasan). Di suhu tinggi ini, terjadi reaksi sintering antar partikel, membuat pelet menjadi keras, fuerte, dan berpori. Pelet yang dihasilkan seragam, mudah ditangani, dan menjadi bahan baku utama yang sangat efisien untuk blast furnace modern. Proses membuat pelet yang bagus itu butuh presisi; kadar air, kecepatan putar, dan suhu indurasi harus pas. Kalau tidak, pelet bisa remuk di perjalanan atau di dalam tungku.
2. Sintering: Alternatif untuk Partikel Halus dan Debu
Metode lain yang umum adalah sintering. Ini terutama digunakan untuk mengolah partikel bijih yang sangat halus, debu pabrik, atau konsentrat yang tidak cocok untuk pelet. Campuran material halus (bisa termasuk konsentrat, bijih berukuran kecil, kapur/dolomit sebagai flux, dan coke breeze/bubuk kokas sebagai bahan bakar) disusun di atas sebuah “pallet” bergerak. Campuran ini kemudian dilewatkan melalui zona pembakar (ignition hood) dimana permukaannya dinyalakan. Api kemudian “menjalar” ke bawah melalui lapisan material, dibantu oleh hembusan udara dari bawah. Suhu mencapai sekitar 1200-1300°C (di bawah titik leleh besi). Pada suhu ini, permukaan partikel meleleh sedikit dan menyatu (sinter) membentuk gumpalan berpori yang disebut sinter cake. Setelah dingin, sinter cake ini dihancurkan dan disaring menjadi ukuran yang sesuai untuk blast furnace (biaa 5-50mm).
Sinter tidak serapuh pelet dan bentuknya kurang seragam, tapi tetap menjadi bahan isian blast furnace yang penting, terutama untuk mengolah kembali limbah halus. Bau khas proses sintering itu sulit dilupakan bagi siapa pun yang pernah bekerja di pabrik besi!
Baik pelet maupun sinter memiliki keunggulan: ukurannya seragam (relatif), kuat sehingga tidak hancur saat ditumpuk atau dimasukkan ke tungku, dan yang terpenting, berpori. Porositas ini memungkinkan gas reduktor (dari bawah) mengalir lancar ke seluruh bagian isian tungku, sehingga reaksi reduksi bisa terjadi secara efisien dan merata. Memilih antara berinvestasi di pabrik pelet atau pabrik sinter seringkali jadi keputusan strategis perusahaan, berdasarkan jenis bijih utama, biaya investasi, dan ketersediaan bahan baku tambahan.
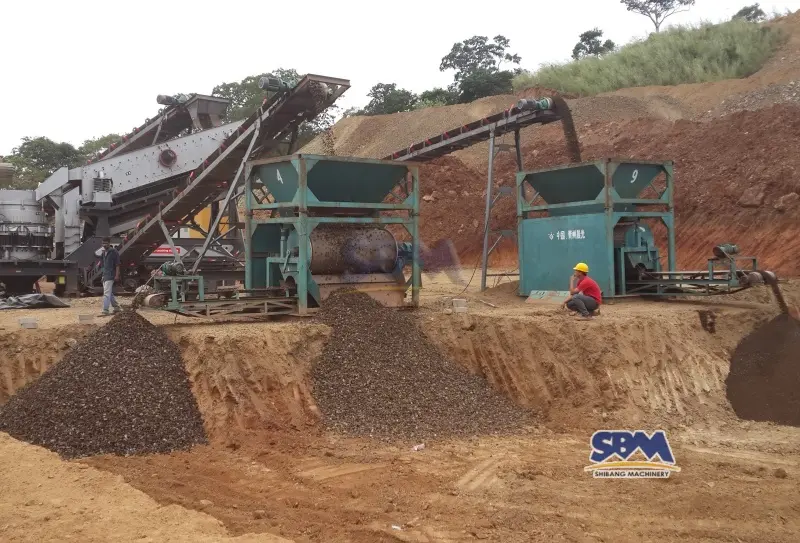
Nivel 4: Reduksi – “Mengambil Oksigennya, Menjadi Logam”
Inilah jantung sebenarnya dariproses pengolahan bijih besi: mengubah bijih besi (terutama oksida besi) menjadi logam besi dengan cara mengambil oksigennya. Proses reduksi ini adalah inti dari segalanya. Ada dua jalur utama yang berkembang di industri:
Blast Furnace (Tungku Tiup): Sang Raksasa Tradisional
Ini masih menjadi metode paling dominan secara global. Bayangkan sebuah menara raksasa (blast furnace) yang tingginya bisa puluhan meter. Dari atas, dimasukkan berlapis-lapis: umpan (bisa pelet, sinter, atau kadang bijih ukuran tertentu), kokas (batu bara yang sudah diproses, berfungsi sebagai bahan bakar sekaligus sumber karbon untuk reduksi), dan flux (batu kapur/dolomit, untuk mengikat pengotor). Dari bagian bawah, ditiupkan udara panas (bisa mencapai 1200°C) yang diperkaya oksigen. Di dalam tungku yang panas menyala-nyala ini, terjadi serangkaian reaksi kimia yang kompleks:
- Kokas (C) bereaksi dengan oksigen (O₂) membentuk karbon monoksida (CO).
C + O₂ -> CO₂
, laluCO₂ + C -> 2CO
- Gas CO yang panas ini naik ke atas melalui lapisan bahan isian.
- CO bereaksi dengan bijih besi (misal Hematit, Fe₂O₃), mengambil oksigennya dan mereduksinya menjadi besi logam cair (Fe).
3CO + Fe₂O₃ -> 2Fe + 3CO₂
(sederhananya). - Flux (kapur) bereaksi dengan pengotor utama dalam bijih (seperti silika SiO₂ dan alumina Al₂O₃) membentuk terak cair (escoria) yang lebih ringan.
CaO + SiO₂ -> CaSiO₃
(terak). - Besi cair (yang disebut pig iron atau besi kasar, mengandung karbon tinggi ~4% dan pengotor lain seperti Si, Mn, P) terkumpul di dasar tungku.
- Terak cair, karena lebih ringan, mengapung di atas besi cair.
- Secara berkala, besi cair dan terak cair dikeluarkan dari tungku melalui lubang tap (tapping hole) yang berbeda. Suasana di sekitar blast furnace saat tapping itu spektakuler (dan panas sekali!) – semburan api dan logam cair yang menyala-nyala. Pig iron inilah bahan dasar untuk pembuatan baja. Bekerja di dekat blast furnace itu mengajarkan arti kata “intensitas” yang sesungguhnya.
Direct Reduced Iron (DRI) / Sponge Iron: Jalur Alternatif yang Berkembang
Seiring tuntutan lingkungan dan ketersediaan bahan bakar, jalur DRI (Besi Reduksi Langsung) atau Sponge Iron (Besi Spons) semakin populer, terutama di daerah dengan pasokan gas alam melimpah atau yang ingin mengurangi jejak karbon. Proses ini tidak melelehkan bijih. Gas pereduksi (terutama Hidrogen H₂ dan Karbon Monoksida CO), yang dihasilkan dari gas alam (reforming), dialirkan ke dalam reaktor (shaft furnace, rotary kiln, fluidized bed) yang berisi pelet bijih besi atau bijih lumpur (lump ore) berkualitas tinggi. Pada suhu tinggi (biaa 800-1050°C, di bawah titik leleh besi), gas pereduksi ini bereaksi langsung dengan bijih besi, mengambil oksigennya. Fe₂O₃ + 3H₂ -> 2Fe + 3H₂O
o Fe₂O₃ + 3CO -> 2Fe + 3CO₂
.
Hasilnya adalah besi padat berpori (seperti spons, makanya disebut besi spons) dengan kandungan besi sangat tinggi (90-94% Fe) dan kandungan pengotor yang rendah. Produk ini disebut DRI (Direct Reduced Iron) atau jika dipadatkan lebih lanjut menjadi briket panas, disebut HBI (Hot Briquetted Iron). DRI/HBI terutama digunakan sebagai bahan baku premium di Electric Arc Furnace (EAF) untuk pembuatan baja. Keunggulan jalur DRI adalah emisi CO₂ yang secara teori lebih rendah (terutama jika menggunakan H₂ hijau), dan skalanya bisa lebih fleksibel dibanding blast furnace raksasa. Ini adalah area yang sangat dinamis dan menjanjikan untuk masa depan pengolahan mineral besi yang lebih hijau.
Nivel 5: Pembuatan Baja – “Menyempurnakan Sang Logam”
Pig iron dari blast furnace atau DRI dari pabrik reduksi langsung, meski sudah berupa besi, belum cocok untuk kebanyakan aplikasi. Kandungan karbonnya masih tinggi (4% pada pig iron), dan ada berbagai pengotor seperti Silikon, Mangan, Fosfor, dan Belerang. Proses pengolahan bijih besi berlanjut dengan menyempurnakan logam ini menjadi baja, yaitu paduan besi dengan kadar karbon yang dikontrol (biaa di bawah 2%) dan pengotor yang diminimalkan.
1. Basic Oxygen Furnace (BOF): Si Cepat dan Efisien
Metode ini adalah yang paling umum digunakan di dunia, terutama menggunakan pig iron cair sebagai bahan baku utama (biaa >70-80%), ditambah besi tua (scrap) dan sedikit flux. Prosesnya cepat dan intensif! Pig iron cair dituang ke dalam konverter BOF (sebuah wadah besar berbentuk buah pir). Lalu, sebuah lance (pipa) diturunkan dan menghembuskan oksigen murni (99%+) dengan kecepatan sangat tinggi ke permukaan logam cair. Oksigen ini bereaksi sangat eksotermik (menghasilkan panas) dengan karbon dan pengotor dalam pig iron.
- Karbon (C) terbakar menjadi gas CO/CO₂.
- Silikon (Si), Mangan (Mn), Fosfor (P) juga teroksidasi.
- Kapur (CaO) yang ditambahkan bereaksi dengan oksida-oksida pengotor (terutama SiO₂ dan P₂O₅) membentuk terak yang mengapung.
Proses ini hanya memakan waktu sekitar 15-25 menit per “charge”! Suhunya bisa mencapai 1700°C. Dengan mengontrol jumlah oksigen dan waktu, komposisi baja bisa diatur dengan sangat presisi. Setelah pengambilan sampel dan analisis cepat memastikan komposisi tepat, baja cair kemudian dituang ke dalam ladle (panci tuang) untuk proses penuangan berikutnya. Kecepatan BOF ini benar-benar luar biasa menyaksikannya.
2. Electric Arc Furnace (EAF): Sang Fleksibel Berbahan Bakar Listrik
Electric Arc Furnace (EAF) semakin populer, khususnya di “mini-mills”. Proses ini mengandalkan besi tua (scrap >90%) atau campuran scrap dan DRI/HBI sebagai bahan baku utama. Sumber panasnya berasal dari listrik tegangan tinggi yang dialirkan melalui elektroda grafit raksasa di atas tungku berbentuk mangkuk.
Busur listrik antara elektroda dan bahan baku menghasilkan panas ekstrem (>3000°C) yang mencairkan material cepat. Penyempurnaan baja cair melibatkan:
- Penembakan oksigen: Membakar pengotor & mengatur karbon.
- Penambahan bubuk arang: Menyesuaikan kadar karbon.
- Penambahan flux (kapur): Membentuk terak penampung pengotor.
Keunggulan EAF:
- Fleksibel: Operasi start/stop mudah.
- Berbasis daur ulang: Dominan scrap metal.
- Emisi CO₂ lebih rendah: Terutama dengan energi terbarukan.
- Suara khas: Dengungan busur listriknya intens (perlu pelindung telinga).
Produk akhir EAF maupun BOF adalahbaja cair berkomposisi spesifik (ejemplo: baja karbon rendah). Baja ini kemudian diproses diMesin Penuangan Kontinu (CCM) untuk membeku menjadi:
- Slab (lempeng tebal untuk pelat/pipa)
- Bloom (kotak besar untuk profil struktural)
- Billet (kotak kecil/bulat untuk batang/kawat)
Produk setengah jadi ini selanjutnya diolah melalui pengerolan atau penarikan menjadi produk baja akhir.n panas (hot rolling), pengerolan dingin (cold rolling), penarikan (drawing), atau proses lain menjadi berbagai macam produk baja akhir yang kita kenal: pelat kapal, pipa saluran, batang beton (rebar), kawat, lembaran otomotif, profil bangunan, dan masih banyak lagi. Proses pengolahan bijih besi yang panjang dan kompleks akhirnya bermuara pada produk-produk yang membentuk infrastruktur kehidupan kita.
Kembali ke Awal: Kenapa Pemilihan Mesin Penghancur Begitu Krusial?
Sebagai orang yang setiap hari berurusan dengan mesin penghancur dan pabrik pengolahan, saya tidak bisa cukup menekankan betapa pentingnya fondasi yang kuat.Proses pengolahan bijih besi dimulai dari penghancuran yang efektif. Jika tahap ini bermasalah, efek berantainya akan terasa sampai ke ujung proses.
- Rompe mandíbulas: Ini adalah garda terdepan. Dia harus tangguh, andal, dan mampu menahan kejutan (impacto) dari bongkahan besar yang masuk. Pengalaman di lapangan mengajarkan bahwa kekuatan frame, kualitas baja rahang (placa de mandíbula), dan sistem penyesuaian yang mudah adalah kunci. Seperti unit PE Series kami yang didesain untuk beban berat dan kondisi tambang yang keras. Kalau jaw crusher sering macet atau cepat aus, seluruh ritme pabrik akan kacau. Investasi di jaw crusher yang bagus itu seperti membeli pondasi rumah yang kuat.
- Trituradora de cono: Setelah di”gebuk” oleh jaw crusher, cone crusher bertugas menghasilkan produk akhir penghancuran yang halus dan berbentuk baik. Untuk bijih besi yang abrasif, ketahanan aus adalah segalanya. Mantel (manto) dan cekung (cóncavo) harus terbuat dari baja mangan tinggi yang tahan lama. Efisiensi penghancuran juga vital untuk menghemat energi. Sebuah trituradora de cono yang bekerja optimal akan menghasilkan produk dengan distribusi ukuran yang konsisten, yang sangat penting untuk kinerja ball mill dan proses konsentrasi selanjutnya. Pemilihan cone crusher yang salah bisa membuat biaya penggantian wear part membengkak dan konsumsi energi melonjak. Pengolahan mineral besi yang efisien dimulai dari sini.
Memilih mesin bukan hanya soal spesifikasi di kertas. Ini tentang memahami karakter bijih lokal, kapasitas yang dibutuhkan, dan dukungan purna jual yang andal. Kami sering melihat pelanggan yang awalnya tergiur harga mesin murah, tapi akhirnya menghabiskan biaya lebih banyak untuk perbaikan dan downtime. Keandalan adalah segalanya dalam menjagaalur produksi bijih besi tetap mengalir lancar dan menguntungkan.
Cubrir: Sebuah Perjalanan Panjang yang Mengagumkan
Entonces, Apa proses pengolahan bijih besi? Ini adalah sebuah saga industri yang epik. Dari bongkahan batu keras dan tak berbentuk di dasar tambang, melalui serangkaian transformasi fisik dan kimia yang kompleks, hingga akhirnya menjadi baja kuat yang membentuk tulang punggung peradaban modern. Setiap tahap – penghancuran, penggilingan, pemisahan, aglomerasi, reduksi, pemurnian – membutuhkan pengetahuan mendalam, teknologi canggih, dan peralatan yang handal.
Memahamitahapan pengolahan bijih besi secara utuh bukan hanya urusan insinyur atau manajer pabrik. Ini adalah kunci untuk membuat keputusan investasi yang cerdas, mengoptimalkan efisiensi operasional yang berdampak pada biaya produksi, meminimalkan dampak lingkungan, dan pada akhirnya, memastikan keberlanjutan bisnis. Di SBM China, menjadi bagian dari perjalanan ini dengan menyediakan mesin penghancur yang menjadi tulang punggung tahap awal proses, adalah suatu kehormatan dan kebanggaan. Kami menyaksikan langsung bagaimana mesin yang andal dan efisien dapat menjadi katalisator kesuksesan operasipengolahan mineral besi pelanggan kami.
Jika Anda sedang merencanakan pabrik baru, mengekspansi kapasitas, atau sekadar ingin mengoptimalkan kinerja fasilitas penghancur yang ada, jangan ragu untuk berdiskusi dengan kami. Tim teknis kami yang berpengalaman siap mendengarkan tantangan spesifik Anda dan merekomendasikan solusi terbaik yang didukung oleh teknologi terkini dan komitmen layanan penuh. Mari bersama-sama membangun industri pengolahan mineral yang lebih kuat, efisien, dan berkelanjutan!
Preguntas frecuentes: Jawaban dari Pengalaman Lapangan
1. Apa saja produk antara dan akhir utama dari rantai pengolahan ini?
- Produk Antara: Konsentrat Bijih Besi (bubuk halus kaya besi), Pelet, Sinter, Besi Kasar (Pig Iron – cair/padat), Besi Spons (DRI/HBI – padat).
- Produk Akhir Utama: Baja dalam berbagai bentuk (Slab, Bloom, Billet, Pelat, Batang/Kawat Rebar, Pipa, Profil Struktural, Lembaran Tipis, dll).
2. Kenapa tidak bisa langsung memasukkan konsentrat halus ke blast furnace?
- Sumbatan Aliran Gas: Bubuk halus akan memadat dan menyumbat ruang antara bahan isian, menghalangi aliran gas reduktor (CO) dari bawah ke atas. Efisiensi reduksi turun drastis.
- Fluidisasi: Gas bertekanan bisa menyebabkan bubuk halus berperilaku seperti fluida (terfluidasi), membuat operasi tidak stabil dan berbahaya.
- Distribusi Panas Tidak Merata: Reaksi tidak terjadi secara homogen.
- Kehilangan Material: Bubuk halus mudah terbawa gas keluar cerobong (dust loss). Pelet/sinter menyelesaikan semua masalah ini dengan ukuran seragam, kekuatan, dan porositasnya.
3. Apa kelebihan dan kekurangan Blast Furnace (BF) vs Direct Reduction (DR)?
- Blast Furnace (BF):
- Kelebihan: Kapasitas sangat besar (ekonomis skala), teknologi matang, bisa menggunakan berbagai umpan (pelet, sinter, lump ore), pig iron cair langsung ke BOF.
- Déficit: Investasi sangat besar, ketergantungan tinggi pada kokas (mahal, emisi tinggi), emisi CO₂ sangat signifikan, proses kontinu sulit dihentikan.
- Direct Reduction (DR):
- Kelebihan: Tidak butuh kokas (gunakan gas alam/hidrogen), emisi CO₂ potensial lebih rendah (terutama dengan H₂ hijau), investasi lebih kecil (skala lebih fleksibel), produk DRI/HBI rendah pengotor (premium untuk EAF).
- Déficit: Membutuhkan bijih/pelet kualitas tinggi (Fe tinggi, rendah pengotor), ketergantungan pada gas alam/reduktor, produk padat (perlu dilebur lagi di EAF), kapasitas umumnya lebih kecil dari BF raksasa.
4. Apakah satu jenis crusher bisa menangani semua jenis bijih besi?
Sangat tidak disarankan! Bijih besi memiliki karakteristik berbeda:
- Kekerasan (Dureza): Bijih sangat keras (misal Magnetit keras) membutuhkan crusher dengan gaya kompresi kuat seperti Jaw dan Cone Crusher. Impact crusher mungkin cepat aus.
- Abrasivitas (Abatría): Bijih abrasif membutuhkan wear part (seperti jaw plate, manto, cóncavo) dari material sangat tahan aus (baja mangan tinggi). Desain ruang penghancur juga berpengaruh.
- Kandungan Lempung (Humedad & Clay): Bijih basah atau mengandung lempung bisa menyumbat crusher tertentu. Kadang perlu pre-screening atau feeder khusus.
- Ukuran Umpan & Produk yang Dibutuhkan: Menentukan jenis crusher (primer, sekunder, tersier) dan konfigurasinya. Pemilihan yang tepat berdampak besar pada biaya operasi dan hasil akhir. Konsultasi dengan ahli dan uji coba di lab/pilot plant sangat penting.
5. Apa tantangan tersulit yang sering dihadapi di pabrik pengolahan bijih besi?
- Fluktuasi Kualitas Bijih: Bijih dari satu tambang pun kualitasnya bisa berubah-ubah, memaksa penyesuaian proses terus-menerus. Butuh sistem kontrol yang tanggap.
- Biaya Energi Tinggi: Tahap penggilingan (molienda) dan blast furnace sangat boros energi. Efisiensi energi adalah fokus utama.
- Pengelolaan Limbah: Volume tailing (limbah hasil konsentrasi) dan slag (terak) sangat besar. Penanganan, penyimpanan, dan pemanfaatan kembali (jika mungkin) adalah tantangan lingkungan dan biaya.
- Dampak Lingkungan: Emisi CO₂ (terutama dari BF), emisi partikel, penggunaan air, dan gangguan lahan.
- Biaya Perawatan & Ketersediaan Mesin: Mesin di lingkungan abrasif dan korosif cepat aus. Downtime untuk perawatan harus diminimalkan. Keandalan mesin penghancur krusial.
- Fluktuasi Harga: Harga bijih besi dan baja sangat fluktuatif, mempengaruhi profitabilitas.
6. Arah perkembangan teknologi pengolahan bijih besi ke depan?
- Dekarbonisasi: Ini yang paling panas! Fokus pada:
- DR berbasis Hidrogen Hijau (H₂-DRI): Mengganti gas alam dengan H₂ yang dihasilkan dari elektrolisis air menggunakan energi terbarukan. Target nol emisi karbon pada proses reduksi.
- Peleburan EAF berbasis Listrik Hijau: Menggunakan listrik dari sumber terbarukan untuk EAF yang memakai DRI/HBI dan scrap.
- CCUS (Carbon Capture, Utilization, and Storage): Menangkap CO₂ dari gas buang BF/BOF dan menyimpannya atau memanfaatkannya.
- Pemanfaatan Limbah: Meningkatkan pemanfaatan slag sebagai bahan bangunan (pengganti agregat, semen) dan recovery mineral berharga dari tailing.
- Digitalisasi & Otomasi: Pemanfaatan AI, IoT, dan big data untuk optimasi proses real-time, prediksi perawatan mesin (mantenimiento predictivo), peningkatan kualitas dan efisiensi. Sensor pada crusher dan conveyor bisa memantau getaran, suhu, beban untuk mendeteksi masalah dini.
- Proses yang Lebih Efisien Energi: Pengembangan teknologi grinding yang lebih hemat energi, proses reduksi alternatif yang lebih efisien, dan optimasi penggunaan panas buang.
- Pengurangan Penggunaan Air: Sirkulasi air tertutup (close loop) dalam proses, teknologi dewatering tailing yang lebih baik.
Oficina central
Whatsapp:+8615225176731
Correo electrónico: [email protected]
DIRECCIÓN: No. 1688, Camino del este de Gaoke, Nuevo distrito de Pudong, Llevar a la fuerza, Porcelana.
Sitio web: https://www.mill-sbm.com/