E-mail: [email protected]
Minerai de fer écrasé
Maison » Pierre écrasée » Minerai de fer écrasé
Main Contents
Look, we all know where the steel in those skyscrapers and cars comes from – iron ore. But hauling that raw rock straight from the pit to the blast furnace? Forget it. It’s useless. Lereal magic, lereal value unlock, happens when you crush it properly.Crushed iron ore isn’t just smaller lumps; it’s the foundation. Get this step wrong, and you’re fighting an uphill battle – clogged screens, overloaded mills, poor recovery, and money literally vanishing into your tailings dam. I’ve spent decades in the trenches of mineral processing, and I can tell you this: optimizing your crushing circuit is the single biggest lever you have for boosting profitability. Let’s cut through the theory and talk brass tacks about gettingcrushed iron ore production dialed in.
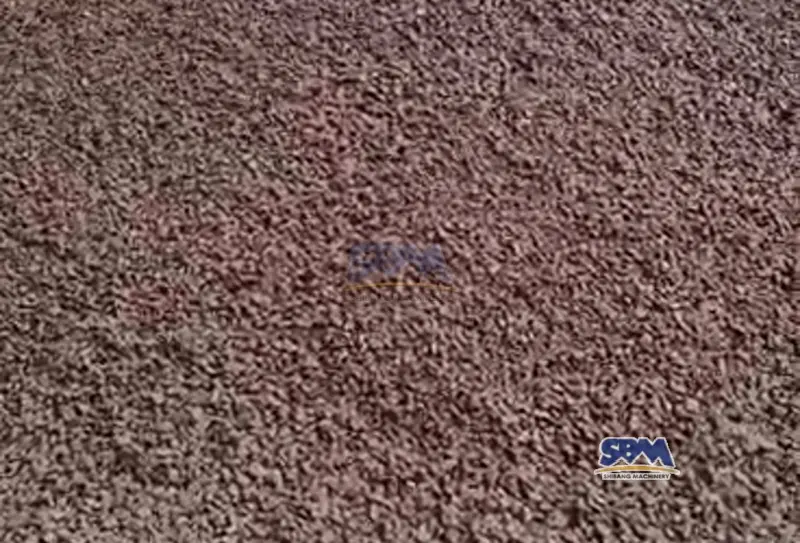
What Exactly Is Crushed Iron Ore? (And Why Size Matters More Than You Think)
Alright, let’s be crystal clear.Crushed iron ore is your raw hematite or magnetite, run through the wringer – a jaw, a cone, maybe an impactor – to bust it down from boulders the size of a small car into manageable fragments. But here’s the kicker: “crushed” isn’t one size fits all. Are you feeding a blast furnace that needs specific lump-to-fines ratios? Running a pellet plant screaming for finely ground feed? Or maybe prepping for magnetic separation? Each downstream process hasvery specific demands on thatcrushed iron ore size distribution. Screw up the PSD (Particle Size Distribution), and you’re instantly handicapping the next stage. The goal? Liberate those precious iron minerals (hematite, magnetite) from the worthless gangue rock as cleanly and efficiently as possible. Liberation starts with the crack of the crusher.
Why Skimping on Crushing is Your Fastest Route to Lost Profits?
Think of poor crushing like trying to unlock a vault with a plastic spoon. It just doesn’t work. Here’s why investing sweat and smart tech into youriron ore crushing pays off tenfold:
- Liberation is King: If your crushers aren’t busting the rock along the natural grain boundaries, those valuable iron particles stay locked up tight inside the waste rock. No amount of fancy downstream kit will free them efficiently. Good crushing = good liberation = higher recovery. Simple as that.
- Surface Area is Your Friend (and Enemy): Smaller particles mean WAY more surface area exposed. That’s gold for sintering and pelletizing reactions, and absolutely critical for efficient smelting. But crush aussi fine too early? You’ve just created a dust nightmare and wasted energy. Finding that sweet spot is key.
- Consistency is Cash Money: Feeding inconsistent sizes (large chunks + powder) to mills causes chaos and quality issues. Uniform crushed ore ensures stable, profitable downstream operations.
- Flow = Go: Ever tried shoveling basketballs? That’s lumpy ore. Crushed iron ore, sized right, flows like a dream through chutes, hoppers, and onto conveyors. Less bridging, less plugging, less cursing from your operators, more uptime. Plus, it packs denser for cheaper transport.
- Downstream Domino Effect: Get the crushing right, and everything downstream gets easier and cheaper. Mills run smoother, separators work better, screens last longer. Bottlenecks vanish. Throughput climbs. Recovery rates smile. It’s the gift that keeps on giving.
The Crushing Chain: From Pit to Product – Nailing Each Link
Producing top-tiercrushed iron ore is a carefully choreographed dance. Miss a beat, and the whole thing stumbles. Here’s how the pros do it:
1. Écrasement primaire: Where the Big Dogs Eat
Picture massive haul trucks dumping house-sized blocks. This is where you bring the sledgehammer. Concasseurs à mâchoires or massive gyratory crushers live here. Their job? Pure, unadulterated force. Smash those monsters down to something manageable, say 6 pour 10 inches. Reliability isn’t just nice here; it’s non-negotiable. If your primary goes down, the whole plant grinds to a halt. That’s why we obsess over robust builds and designs you can actually maintain without needing a PhD in contortionism. Seen too many “cheap” primaries turn into money pits. Don’t be that guy.
2. Secondary Crushing: Shaping Up & Sizing Down
Primary output is still way too chunky for most concentrators. Enter the concasseur à cône. This is where the finesse starts (relatively speaking!). Cones (especially modern hydraulic multi-cylinder beasts like our HPT series – check how they handle tough stuff like river pebble too at mill-sbm.com
) are the workhorses. They take that fist-sized rock and crunch it down further, typiquement 1 pour 3 inches. Why cones rule here? Great capacity, produce a cubical product (less flaky crap that causes issues later), and their automation keeps sizing tight and consistent. Impact crushers can play if your ore is softer, but watch wear costs like a hawk.
3. Tertiary/Quaternary Crushing: The Fine Art of Reduction
Need your crushed iron ore very fine for pelletizing or better grinding? This is where specialized equipment steps in. Finer cone crushers or High-Pressure Grinding Rolls (HPGR) handle this job. HPGRs work uniquely – they squeeze rock between heavy rollers under huge pressure, creating tiny cracks inside the material. This reduces particles to under half an inch (<0.5″) and can dramatically improve later grinding efficiency (using much less power!). It’s exact breaking, requiring smart controls and precise setup. While not always necessary, when you need ultra-fine material, HPGRs deliver a major improvement.
4. Screening: The Unsung Hero (Don’t Ignore It!)
You can’t control what you don’t track. Screening happens all through a crushing setup. Vibrating screens are the quality checkers. They strictly separate the crushed iron ore into “ready to use,” “too large – send back for recrushing!” (closed-loop system – vital!), et “too fine – may skip ahead.” Good screening is utterly important. It prevents crushers from re-crushing rocks they already broke (wasting huge power), shields later equipment, and guarantees you meet that perfect size target. Cut corners on screens or upkeep? Expect trouble and off-grade material.
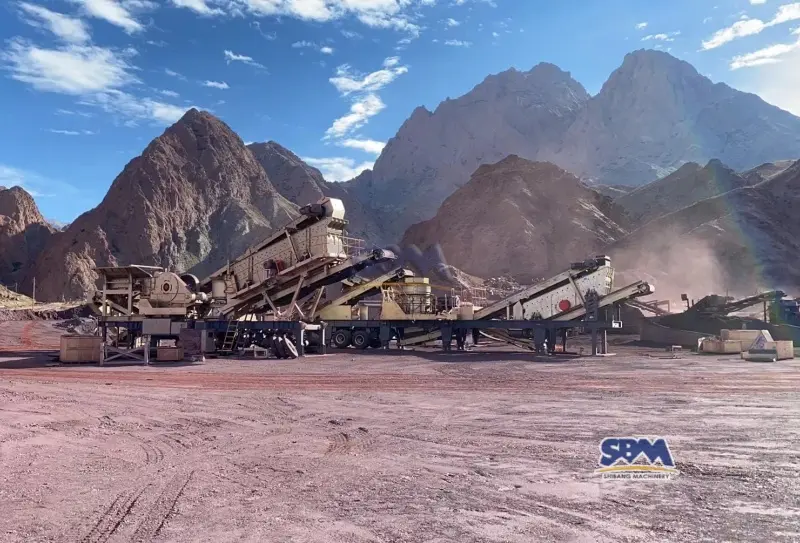
Picking Your Crusher: It’s Like Choosing a Workhorse – Match the Beast to the Task
Throwing any old crusher at yourminerai de fer is a recipe for disaster. Choosing wisely hinges on knowing your enemy (the ore) and your goals:
- Ore Personality: Is it harder than a banker’s heart? Abrasive like sandpaper? (Think: Wear costs!). Tough, abrasive ore demands tanks like gyratories or cones built for punishment. Softer stuff might let you consider impactors, but check wear rates constantly.
- Feed & Finish: What size rocks are you dumping in? What size must come out? This dictates the stage (primaire, secondaire, tertiary) and the crusher type’s sweet spot. Don’t ask a mouse to eat an elephant.
- Tonnes Matter: Can the crusher handle your plant’s appetite? Under-sizing leads to bottlenecks; oversizing wastes capital and energy.
- Stickiness Factor: Got damp, clayey ore? That stuff loves to plug. You need crushers designed with good clearances and maybe even built-in anti-clogging tricks. Nothing kills flow like a sticky plug.
- Shape Counts: Need nice, chunky cubes for pelletizing? Cones are your friend. Impactors give a more variable shape. Know what your downstream process craves.
- Total Cost of Ownership (TCO): Look beyond the sticker price! Factor in power bills (big one!), liner wear costs (massive for hard ore!), maintenance downtime, and ease of service. A cheap crusher can be the most expensive machine in your plant if it eats liners or breaks down constantly.
Let’s Talk Crushers: Real-World Strengths & Quirks for Iron Ore
Forget dry tables, let’s chat specifics like we’re standing by the circuit:
- Concasseur à mâchoires (Primary): Simple, tough, relatively cheap upfront. Loves big rocks. Downside? Product can be a bit slabby (not super cubic), wear costs on hard ore can bite, and they need a big footprint. Great entry point, reliable, but mind the liner changes.
- Concasseur giratoire (Primary): The undisputed king of raw tonnage for massive operations. Handles huge feed, robust as hell. But… expensive, complex to maintain, needs serious foundations, and liner changes are an event. You buy this for sheer capacity over decades.
- Concasseur à cône (Secondaire / tertiaire – Par exemple, HPT): The versatile MVP for most plants. Excellent capacity, produces that desirable cubical product, energy-efficient for the size reduction it does. Modern hydraulics (like ours) auto-adjust for wear and optimize performance. Handles hard/abrasive ore well, but liner costs are still a factor. This is where you spend time optimizing.
- Concasseur à percussion (Secondaire): Often cheaper upfront, good for softer/less abrasive ores, can produce a decent spec product. BUT… wear costs on hard/abrasive minerai de fer? Brutal. Hammers and aprons get chewed up fast. Particle shape can be less predictable. Proceed with caution and a big wear parts budget if your ore is tough.
- HPGR (Tertiary/Quaternary): The new(ish) kid with serious potential. Unbeatable energy efficiency for fine crushing. Creates micro-cracked particles that make downstream grinding WAY easier (huge energy saver!). Great product fineness control. Complex to operate/maintain, sensitive to feed fluctuations, and capital cost is high. But the operational savings (power, grinding media) can be massive. Worth serious consideration for new plants or upgrades needing fine feed.
Quality Control: Not Just a Box to Tick – It’s Profit Assurance
Producing mountains ofcrushed iron ore means nothing if it’s inconsistent junk. Here’s what we watch like hawks:
- PSD is Gospel: Sieve analysis isn’t paperwork; it’s your profit report card. Is the lump/fine ratio perfect for the BF? Are the fines too coarse or too fine for the pellet plant? Consistent PSD = stable downstream = maximum yield. Run these tests religiously.
- Chemistry (The Head Grade): Crushing doesn’t change chemistry, but consistently feeding the crusher helps predict what hits the concentrator. Spot checks catch dilution from waste rock sneaking in – dilution you pay to crush and process for zero return!
- Moisture: The Flow Killer: Too much water? Kiss smooth handling goodbye. Expect sticky plugs in chutes and bins. Plus, you’re paying to ship water and burn energy drying it later. Manage it.
- Tramp Metal & Nasties: Bits of shovel tooth, drill steel, or rogue bolts? They wreck downstream equipment (especially expensive grinding mills!). Metal detectors and magnets on the conveyor après crushing are cheap insurance. Excessive clay? Screams pre-washing might be needed.
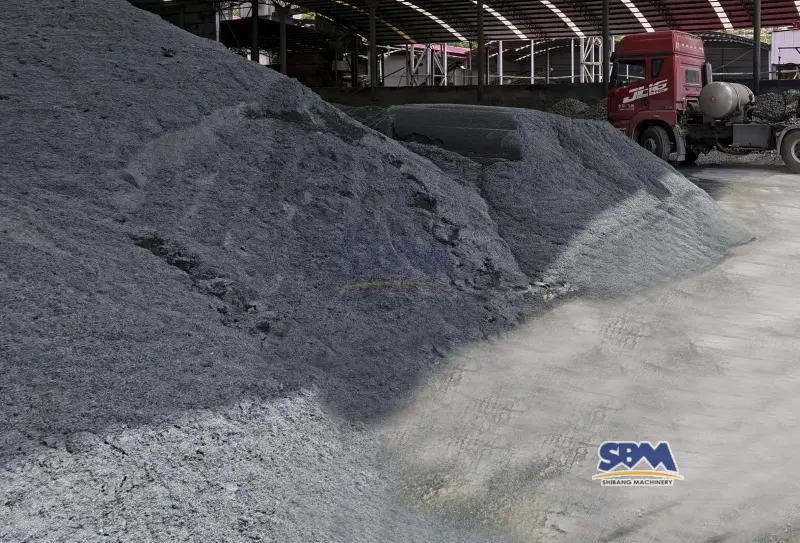
Beyond the Red Dirt: Why Our Iron Ore Know-How Cracks Other Rocks Too
Sure, iron ore crushing is our core business, but the core ideas? They work everywhere. Take river pebble. Breaking down that hard, lisse, tough stuff for top-grade concrete sand or construction stone? It’s a major challenge, just like crushing hard hematite. The exact same crushers that shine in our iron ore setups – especially strong, effective multi-cylinder hydraulic cones (yes, like our HPT series – see them handle river pebble specifically at mill-sbm.com) – are perfect here too. The job is the same: break down hard, tough material well, while keeping the shape right and reducing wear. The methods we perfected on iron ore work exactly here. Good crushing is just good crushing. Period.
Field-Proven Hacks: Squeezing Every Ounce of Efficiency from Your Crush
From decades solving field problems and refining equipment, here’s proven operational advice:
- Closed Circuit is Non-Negotiable: Recycling oversize material back through the crusher is fundamental. It maximizes crusher utilization (they hate running empty!), prevents over-crushing of fines, and gives you real control over product size. Open circuit crushing is just lazy and wasteful.
- Wear Parts: Manage Them or They’ll Manage You: Crusher liners (mantles, concaves, jaw dies) are expensive consumables. Don’t wait for them to fall off! Track wear rates meticulously. Schedule changes proactively based on data, not disaster. Use premium alloys matched to your ore’s abrasiveness. Downtime for liner changes is pure lost revenue – plan it, optimize it, execute it fast.
- Consistent Feed = Peak Performance: Maintain steady material flow into crushers. Too little feed causes vibration and uneven wear. Too much risks jams and damage. Invest in quality feeders—they prevent costly operational issues.
- Automation: Use It or Lose It: Modern crushers (especially cones and HPGR) have brains. Use their automation! Let it adjust settings for wear compensation, monitor power draw (a key health indicator), control feed rates, and protect the machine. Ignoring this is leaving free performance and protection on the table.
- PM is Cheaper Than Breakdowns: This isn’t rocket science, but it’s amazing how often it’s ignored. Stick religiously to lubrication schedules. Check belt tensions and alignments. Listen for new vibrations (get sensors!). Inspect components. A few hours of planned PM beats days of unplanned chaos every single time.
- Track the Juice: Crushing gulps power. Monitor kWh per tonne crushed. If that number starts creeping up, sound the alarm! It usually means worn liners, incorrect crusher settings, feed problems, or mechanical issues. It’s a fantastic early warning system.
The Bottom Line: Crushing Inefficiency is Money Down the Crusher
Poor crushed iron ore production isn’t just inefficient—it actively destroys profits. Here’s where losses happen:
- Major Bottlenecks: Incorrect sizing causes blocked screens, jammed feeders, overloaded mills, and slowed separators. Plant output drops. Revenue disappears.
- Power Bill Nightmares: Poor liberation from bad crushing forces your grinding mills to work way harder (and longer) to free the minerals. Grinding is the single biggest energy hog in the plant. You’re literally burning money because your crushers didn’t do their job well enough.
- Recovery Losses: When iron remains trapped in waste rock after crushing, it’s dumped as tailings. That’s pure profit loss. Better crushing = better mineral liberation = higher yield.
- Wear Part Avalanche: Wrong crusher for the ore? Running it poorly? Expect liner costs to skyrocket. Mechanical failures become frequent. Maintenance budgets explode. Cheap crushers often have the highest operating costs.
- Penalties & Rejections: Deliver crushed iron ore that doesn’t meet the sinter plant’s or pellet plant’s strict size specs? Get ready for price deductions or even rejected loads. Reputation takes a hit too.
Smart investment in suitable crushing technology (durable, efficient, ore-matched) with optimized operation delivers your strongest return on investment:
- ✓ Higher output
- ✓ Lower energy bills
- ✓ Reduced metal loss
- ✓ Decreased maintenance costs
This investment pays back quickly.
Safety: This Ain’t Optional – It’s How We Go Home Alive
Let’s not mince words: Crushing plants are dangerous places. Massive forces, moving parts, poussière, bruit. Safety isn’t a priority; it’s the foundation. Period.
- Energy Isolation (LOTO): Before any crusher maintenance/clearing: 1) Cut ALL power sources (electrical/hydraulic/gravity), 2) Lock/tag controls, 3) Verify zero energy. Never skip steps—complacency causes accidents.
- Machine Guarding: Secure every rotating part, belt, and pinch point with permanent guards. Never remove or bypass them—guards prevent severe injuries.
- Dust Control: Inhaled iron ore dust damages lungs; airborne dust can explode. Mandatory protections: water sprays, ventilation systems, dust hoods, and worker respirators.
- Noise: Protect Your Hearing: These machines roar. Designate hearing protection zones. Enforce wearing earplugs or muffs. Tinnitus is forever.
- Train, Train, Train: Every single person on site needs thorough training – not just on their job, but on site-wide hazards, safe procedures (especially for clearing blockages!), and emergency response. Knowledge is safety armor.
- Strict Procedures: Document step-by-step guides for high-risk tasks (liner changes/blockage removal). Follow them exactly—every time. Carelessness causes fatal accidents.
Where We’re Headed: Smarter, Leaner, Meaner Crushing
The future ofiron ore crushing looks exciting (and efficient!):
- IA & Smarter Equipment: Crushers will self-diagnose problems! By monitoring vibration, temperature, and power use, they’ll predict failures (like worn bearings or liners) before causing stoppages. AI will auto-adjust settings for changing ore hardness. This tech is advancing rapidly.
- HPGRs Gain Ground: Their energy savings, especially on the path to finer grinds, are too big to ignore. Expect wider adoption, particularly in new greenfield projects or major upgrades. The TCO argument is strong.
- Materials Science Wins: Liners that last twice as long? Sign us up! Continuous R&D in ultra-hard, impact-resistant alloys is crucial. Less downtime for changes, lower operating costs.
- Energy Recovery Research: Crushing wastes huge energy as heat/vibration. Can we reuse some? Early concepts exist. Even small savings would be valuable.
- Plant-Wide Brain: Crushing won’t be an island. It’ll be tightly integrated into the mine-to-port digital ecosystem, feeding data and receiving optimizations holistically. Real-time adjustments based on ore characteristics from the pit? Oui, please.
Crushing – The Unsung Hero of Steel
Crushed iron ore. Sounds simple, right? Just break some rocks. But anyone running a plant knows the real story: it’s the absolutely essential starting point for the whole iron and steel industry. Getting the size correct, freeing up as much iron as possible, and keeping things steady needs smart tools, watchful running, and a constant push to do better. From the massive power of the first crusher to the exact breaking of the cone crusher and the careful sorting by the screens – every single step counts.
As the folks building the machines that do this tough job every single day, we get it too. Picking the right crusher – one that’s strong enough, doesn’t waste energy, and keeps running reliably – isn’t just about buying gear. It’s a smart move for your plant’s future earnings. Whether it’s red hematite for the blast furnace or black magnetite for pellets, it all begins with powerful, efficient breaking.
Let’s keep working hard, finding new ways, and sharing what we’ve learned to make crushed iron ore production smarter, safer, and more cost-effective. Because doing things better today literally builds tomorrow’s world. Now, be straight with me – what’s the toughest problem in your crushing setup right now? Always eager to hear about real challenges from the field.