E-pos: [email protected]
Vaste kakebeen -vibrasie -analise: Verbeterende prestasie en lang lewe
Vibration analysis is a critical tool for ensuring the reliability and efficiency of fixed jaw crusher in mining and construction industries. By monitoring and interpreting vibration patterns, operators can detect issues early, reduce unplanned downtime, and extend equipment lifespan. This article explores practical techniques, global case studies, and actionable insights for integrating vibration analysis into your maintenance strategy.
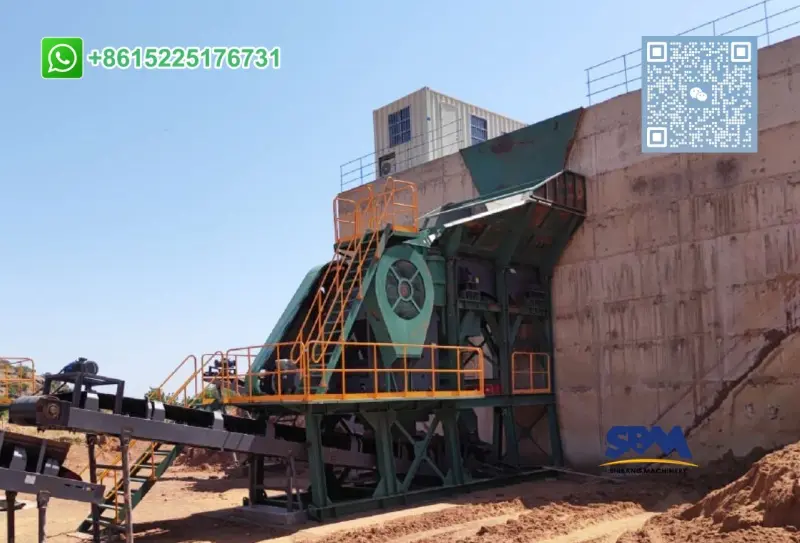
Why Vibration Analysis Matters for Fixed Jaw Crushers
Fixed jaw crushers are robust machines designed to crush hard materials like granite, basalt, en concrete into gravel or aggregates. Egter, their heavy-duty operation generates significant mechanical stress, leading to wear on components like the fixed jaw plate, eccentric shaft, and bearings. Excessive vibration can accelerate component degradation, causing:
- Premature failure of bearings or liners
- Misalignment of the crushing chamber
- Reduced crushing efficiency and uneven output
Byvoorbeeld, a quarry in Australia reported a 30% increase in maintenance costs due to undetected bearing wear in their fixed jaw crusher. Implementing vibration analysis helped them identify imbalances early, saving $120,000 annually in repairs.
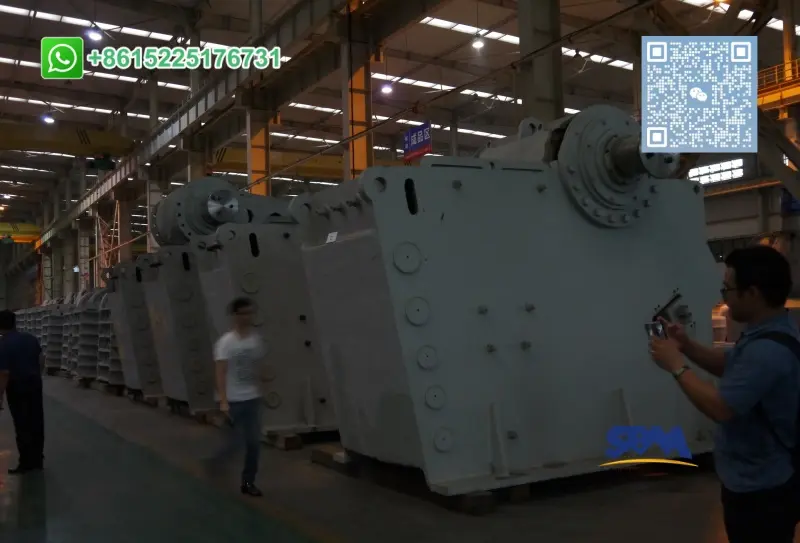
Key Techniques for Effective Vibration Analysis
1. Time-Synchronous Averaging for Rotational Component Monitoring
Fixed jaw crushers rely on rotating parts like the eccentric shaft and flywheel. Time-synchronous averaging (TSA) isolates vibration signals synchronized with shaft rotation, enabling precise detection of irregularities such as:
- Imbalanced flywheels
- Eccentric shaft misalignment
- Worn toggle plates
A study in Brazil used TSA to diagnose a cracked eccentric shaft in a PEX-250×1000 jaw crusher, preventing catastrophic failure.
2. Envelope Spectrum Analysis for Bearing Health
Bearings in fixed jaw crushers are prone to fatigue due to high loads. Envelope spectrum analysis identifies high-frequency vibrations caused by bearing defects, soos:
- Spalling or pitting on raceways
- Cage damage
- Lubrication failures
In a Canadian mining operation, this method detected early-stage bearing wear in a PE-600×900 crusher, reducing replacement costs by 45%.
3. Modal Analysis for Structural Integrity
Fixed jaw crusher frames and jaw plates must withstand intense forces. Modal analysis evaluates natural frequencies and damping ratios to prevent resonance, which can lead to structural cracks. Byvoorbeeld, a German cement plant used modal testing to optimize the design of a PE-1200×1500 crusher, achieving a 20% longer service life.
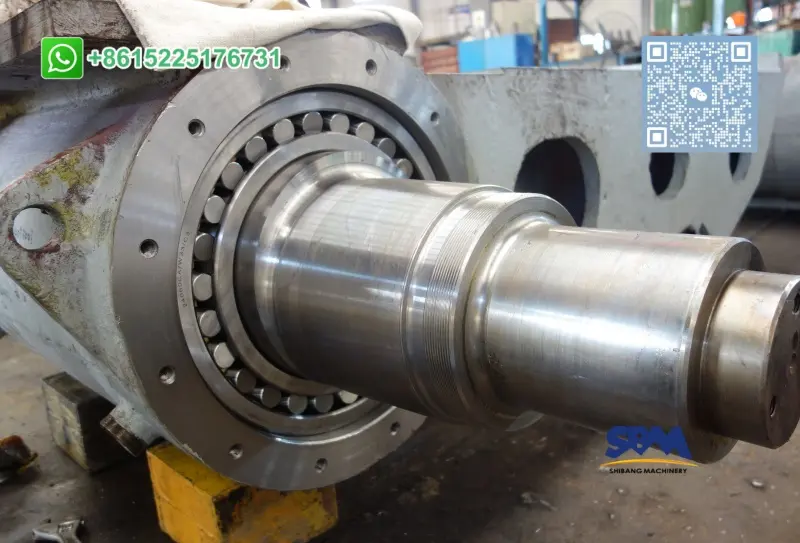
Global Case Studies: Lessons from the Field
Case 1: Reducing Downtime in a U.S. Granite Quarry
A granite processing facility in Texas experienced frequent breakdowns in their fixed jaw crusher due to uneven material feed. Vibration analysis revealed excessive torsional vibrations in the eccentric shaft. By adjusting the feed rate and replacing worn jaw plates, downtime decreased by 60%.
Case 2: Optimizing a Fixed Crusher in South Africa
A gold mine in Johannesburg used vibration diagnostics to address premature wear in their PE-900×1200 crusher. Analysis identified misaligned toggle plates and imbalanced flywheels. Realigning components and upgrading to high-manganese steel jaw plates improved throughput by 25%.
Practical Tips for Implementing Vibration Analysis
- Integrate Sensors Strategically
Mount accelerometers on critical components like the bearing housings, raam, and moving jaw. Wireless sensors offer flexibility for real-time monitoring in harsh environments. - Baseline Data Collection
Establish baseline vibration levels during normal operation. Compare future readings to detect anomalies early. - Combine with Preventive Maintenance
Schedule inspections alongside vibration checks. Byvoorbeeld, inspect the fixed jaw plate and toggle plates every 500 bedryfsure. - Train Operators in Diagnostics
Equip your team with tools like frequency spectrum analyzers and training on interpreting vibration trends.
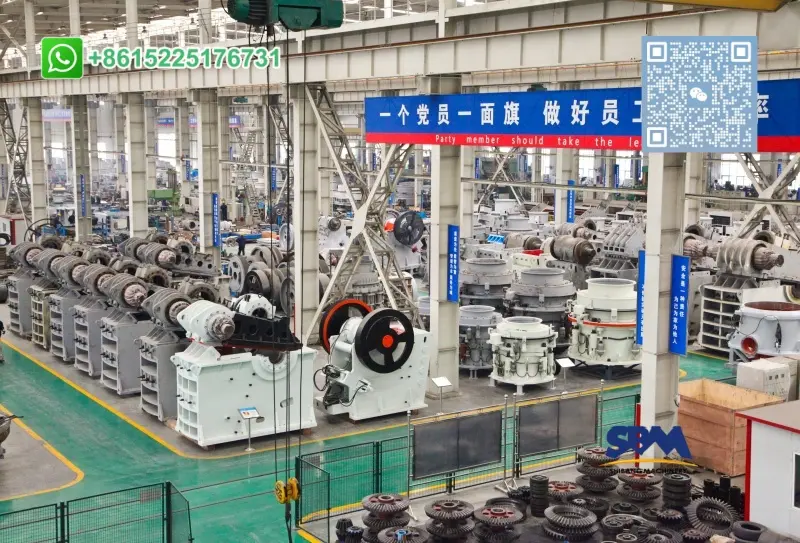
Linking Vibration Analysis to Broader Crusher Management
To maximize the benefits of vibration analysis, pair it with:
- Proper Installation (See: Installing a Jaw Crusher for guidelines)
- Regular Lubrication Protocols
- Material Feed Optimization
Daarbenewens, consider whether a mobile jaw crusher of fixed jaw crusher better suits your project (Compare: Mobile vs Fixed Jaw Crushers). For cost-conscious operations, evaluate Used vs New Jaw Crushers to balance upfront investment and long-term reliability.
Vaste kakebeen -vibrasie -analise
Vibration analysis is not just a technical exercise—it’s a cost-saving strategy that enhances the performance of fixed jaw crushers. By adopting advanced diagnostic techniques and learning from global case studies, operators can minimize downtime, extend component life, and maintain consistent output quality. Start small: implement basic vibration monitoring today, and gradually scale to predictive maintenance models for long-term success.
Hoofkwartierkantoor
Whatsapp:+8615225176731
E-pos: [email protected]
Adres: Geen. 1688, Gaoke East Road, Pudong nuwe distrik, Sjanghai, Sjina.
Webwerf: https://www.mill-sbm.com/