E-pos: [email protected]
Crushed Tuff
Tuis » Fyngemaakte klip » Crushed Tuff
Hoofinhoud
Forget what you think you know about crushed tuff. This rock—formed by ancient volcanoes—is more than just attractive. I’ve seen how this lightweight, fast-draining volcanic material fixes actual job site headaches. Need backfill that won’t crush weak foundations? Want landscaping that survives heavy rains? Need concrete that’s lighter and cheaper to build with? Crushed tuff werk. Dit is 30% lighter than granite (cutting delivery costs), drains exceptionally well (no more ruined bases), and firms up solidly when packed down. Ja, it creates dust and soaks up water in mixes—but learn its ways, and you’ll have a local, earth-friendly partner that beats ordinary options. From supporting tall buildings in Mexico City to decorating dry gardens in Arizona, tuff shows that smart building starts with the earth’s natural strength.
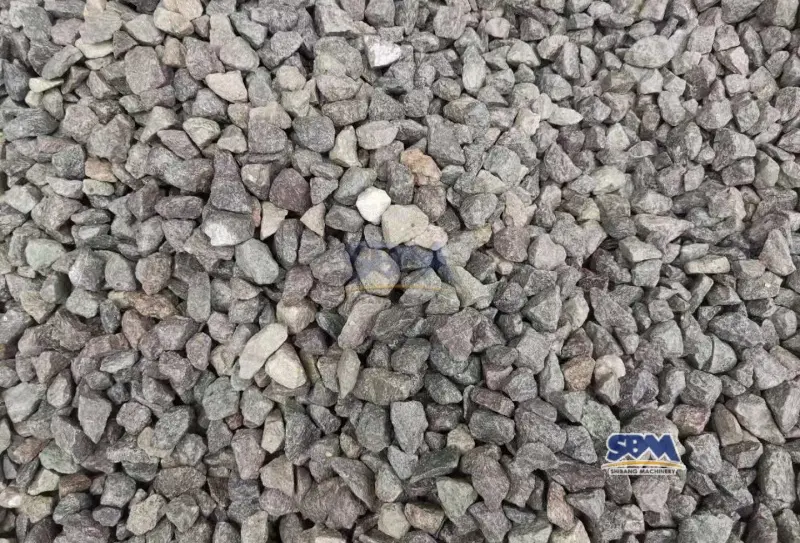
What Exactly Is This Stuff?
Let’s skip the textbook talk. Picture Mount St. Helens erupting – that huge cloud isn’t just smoke. It’s billions of fine ash bits and fist-sized pumice rocks falling everywhere. Jump ahead thousands of years. All that messy debris? Heat, pressure, and mineral-packed groundwater fuse it into rock that’s surprisingly solid but usually softer than graniet. Crushed tuff is just that hardened volcanic ash broken apart again – now by modern crushers – and sorted into useful sizes. It’s not all the same. One pit’s tuff might be dense and gray like old concrete; another’s could be full of holes and rust-red. That difference? It’s not a mistake, it’s personality. You figure out its ways like getting to know a new worker. Using it feels like teaming up with the earth – not always predictable, occasionally tough, but worth it in the end.
Why Crushed Tuff Earns Its Keep: More Than Just Cheap Fill?
Forget the sales brochures. Here’s why this volcanic aggregate gets called back job after job:
- The Weight Advantage: Hauling granite gravel feels like moving lead weights. Tuff rock can be 30-40% lighter. That means fewer truck trips, less diesel burned, and happier workers at day’s end. On that shaky bridge project last fall, engineers required lightweight fill – tuff saved the day, preventing expensive ground reinforcement.
- Drains Like a Sieve: Water pooling under your foundation? Crushed tuff handles saturation easily. Its natural holes and jagged edges create thousands of drainage paths. I’ve watched it absorb heavy rains that turned regular road base into mud. For drainage trenches or behind walls? It’s now my top choice.
- Surprisingly Tough Love: Don’t let the lighter weight fool you. Well-gradedfyngemaakte vulkaniese rots locks together fiercely under compaction. It won’t rut like limestone screenings under heavy equipment. For sub-base under paved areas where frost heave is a nightmare? Its drainage plus compaction is a one-two punch.
- Beauty with Brawn: Landscapers take note. That “crushed sunset” look? Customers love it. From New Mexico’s golden yellows to Iceland’s charcoal blacks, volcanic stone adds natural beauty. Unlike cheap white chips that fade in sun, it keeps its color. Weeds also struggle in its loose surface layer. Pretty and practical.
- The Thermal Trick: Building in hot or cold zones? Tuff’s air pockets work like tiny insulators. It won’t replace boards, but in foundation fills or under heated floors, that extra insulating power matters. Comfort doesn’t have to cost more.
Where Crushed Tuff Shines: Beyond the Spec Sheet?
Forget generic “applications.” Here’s where it consistently outperforms:
- The Foundation Savior: Backfilling tight spots around deep foundations? Heavy soil pushes back hard.Crushed tuff’s lightness cuts side pressure dramatically. On that downtown skyscraper with inches to spare? Engineers demanded tuff backfill. Resultaat? Little settling, less crew stress.
- Landscaping’s Secret Weapon:
- Walkways: Skip muddy stone paths. Use 4 inches of packedtuff base + 2 inches of finecolored tuff op die top. Drains instantly, stays flat, feels gentle underfoot. Onderhoud? Quick yearly rake.
- Dry Streams: Looks real, handles floods. Use 2-4″ chunky tuff for the “stream,” smaller pieces for “banks.” Works like art.
- Fireproof Buffers: Near buildings in fire zones? Volcanic rock won’t burn like wood mulch. Stays clean-looking.
- Lightweight Concrete’s Backbone: Replacing heavy rock withcrushed volcanic stone in floor slabs or wall panels slashes weight. Benefits? Smaller support columns, less steel, faster builds. Concrete crews may complain (it soaks more water!), but savings add up. One parking garage saved 12% on steel costs—thank you, tuff!
- Railroad Ballast (The Right Stuff): Only dense tuff works here. Crushed to sharp edges, it grips tracks tightly and drains better than smooth river rock. Less washed-out tracks, fewer repair crews needed.
- Slope Armor That Breathes: Large tuff chunks (6-12″) protect hillsides needing erosion control + drainage. Unlike solid rock trapping water, tuff lets water pass through, easing pressure on slopes. Stays stable for decades.
The Green Angle: It’s Not Just Virtue Signaling
Sustainability gets thrown around like confetti. Withcrushed tuff, the benefits are tangible:
- Local = Less Truck Fumes: Big tuff deposits exist worldwide: Eastern Oregon, Arizona, Italy’s Tuscany, Kenya’s Rift Valley. Gettingtuff rock from 50 miles away beats hauling granite 200 miles. Just the diesel saved makes your project cleaner. Actual results, not just words.
- Quarrying’s Lighter Touch: Mining and crushing hard granite eats up huge energy.Tuff, being softer? Uses less fuel in loaders and crushers. Machinery lasts longer too (though dust control is crucial – more below). Smaller carbon bill.
- The Ripple Effect: Lightweight fill means smaller retaining walls needing less concrete. Lightweight concrete means slimmer foundations. These savings add up across the whole job. Efficiency built right in.
- Nature’s Abundance: It’s literally ancient volcanic debris. Good quarry practices (restoring sites matters!) use this plentiful but overlooked resource. This eases demand on sand/gravel pits near rivers or wetlands. Smart use of what’s available.
From Bedrock to Build-Ready: The Crusher’s Crucible
Turning ledge tuff into usable aggregate isn’t magic – it’s machinery, sweat, and knowing your rock. Here’s the gritty reality:
1. Face Shot (Maybe)
Is the tuff layer thick and hard? Controlled blasting breaks it into “broken rock” (fist-to-refrigerator-sized chunks). Soft, crumbly tuff? An excavator with a ripper tooth might handle it alone.Dust flies everywhere. Safety goggles aren’t optional.
2. The Haul
Dump trucks rumble, carrying shot rock to the primary crusher. Distance matters – fuel is money.
3. Primary Crushing – The Jaw’s Grip
This is where the big boys play. A massive jaw crusher (think V8 engine meets a trash compactor) smashes boulders down to roughly 6-8 inches.Tuff crushers need robust frames but can often run faster than when chewing granite. Feed size is critical – too big a chunk jams it solid.(Seen SBM China’s jaw crushers handle blocky tuff like champs – serious bite: https://www.mill-sbm.com/products/c6x-jaw-crusher).
4. Secondary Smash – Shaping the Future
Primary crush is too coarse for most uses. Enter the cone crusher or impact crusher.
- Cone Crushers: Giant spinning press. Smashes rock between metal surfaces. Best forhard tuff and consistent sizing. Creates some dust/sand. Wear parts needregular replacements – cost it in.
- Impact Crushers: Hammers slam rock against steel plates. Makessquare-shaped pieces – perfect for strong concrete. Better forsofter tuff. Can be dustier.(SBM’s impact crushers make beautifully shaped tuff aggregate: https://www.mill-sbm.com/products/pfw-impact-crusher).
5. Tersiêre verplettering / Shaping (The Finishing Touch)
Need precise sizes or artificial sand? A Vertical Shaft Impactor (ALMAL) smashes rock-against-rock for exact shaping. Costs more, but vital for premium grades. Read more about tuff sand making plant.
6. Screening – Sorting the Family
Vibrating screens are the unsung heroes. Multiple decks separate the crushed mix into usable fractions:
- 1-1/2″ to 3/4″ (Dreinering, Ballast)
- 3/4″ tot 3/8″ (Konkreet, Base Course)
- 3/8″ aan #4 (Konkreet, Teer)
- Fines (Screened sand substitute, landscaping top dress)
Enemy: Screens clogging (blinding). Worse with damp, clay-rich tuff. Choose screen type (wire or plastic) based on rock hardness and moisture.
7. The Wash Plant (Optional but Often Vital)
Tuff dust is super fine.Concrete plants or fancy landscapes need it clean. Run it through a washer to remove silt/clay. Creates a top-quality product you can sell.Downside: Now you’ve got muddy water – need ponds to settle it out.
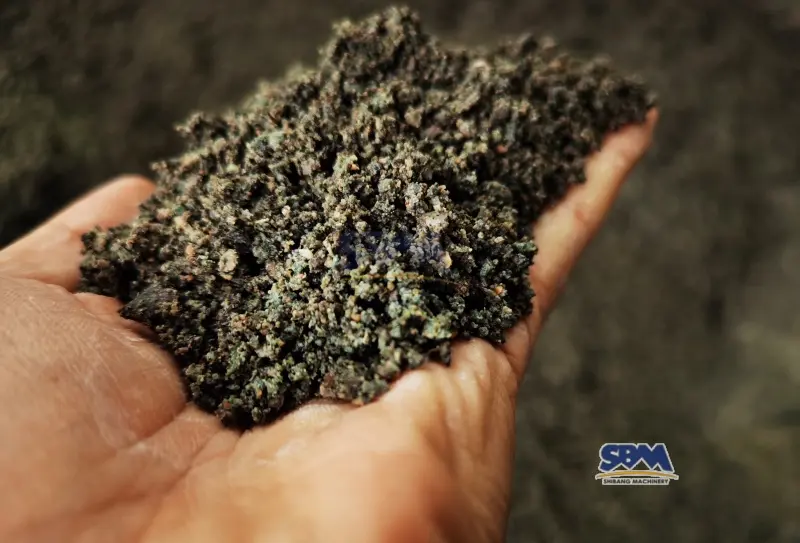
Picking Your Tuff-Crushing Weapon: It’s Personal
Choosing the right crusher setup isn’t abstract – it impacts your bottom line daily. Consider:
- Rock Character: Is your tuff soft and crumbly? A primary impact crusher might handle it solo. Hard and abrasive? Jaw + Cone is the durable workhorse. Abrasion-resistant liners aren’t optional – they’re profit protection.
- End Product Matters: Making top-grade concrete where rock shape is critical? Impakbrekers (HSI or ALMAL) create prized square-shaped pieces. Just needing road base? Cone crusher output may work fine. Know who’s buying your rock.
- Production Size: A small pit selling to landscapers needs less power than one supplying state highway jobs. Match the crusher’sopening size and engine power to your target tons-per-day.Too small? You lose money. Too big? You waste cash.
- Mobility or Monolith?
- Fixed Plant: High volume, long mine life. Higher capital, lower operating cost per ton. Needs solid infrastructure (power, foundations).
- Mobile Crushers: Game-changers. Track-mounted jaw, keël, impact, screen combos. Perfect for smaller deposits, remote sites, or contract crushing moving between pits. Setup in hours, not weeks. Fuel-hungrier per ton, but flexibility is priceless.(SBM China’s mobile lines are beasts – set up on Monday, crushing by Tuesday: https://www.mill-sbm.com/products/k3-series-portable-crushing-plant).
Optimizing the Crush: Where the Profit Hides
Fine-tuning your crushing spread separates the pros from the strugglers:
Factor | Reality Check | Why Your Wallet Cares |
---|---|---|
Feed Discipline | Scalping (pre-screening) finesout before primary crushing is non-negotiable. Fines consume energy without being crushed and jam chambers. | Saves fuel, prevents downtime, protects liners. |
The Gap is God | Jaw CSS (Geslote syinstelling), Cone settings, Impact apron gaps – measure them constantly with feeler gauges. A 1/8″ drift ruins your product curve. | Consistent sizing = premium product prices & less waste. |
Wear Parts Whisperer | Waiting for liners to fall apart is amateur hour. Track tons processed. Schedule changesbefore quality degrades. Worn liners make flaky, out-of-spec product nobody wants. | Maximizes saleable tons, avoids rejected loads, protects crusher internals ($$$). |
Screen TLC | Slack screen tension? Blinding starts. Wrong mesh size? Good product goes to waste. Clean decks, tensioned mesh, correct angles – boring maintenance that prints money. | Maximizes yield per grade ($$$), reduces re-crush. |
Dust Wars | Dry tuff + crushing = dust apocalypse. Water sprays at transfer points, enclosed conveyors, maybe even baghouses aren’t environmental fluff – they’re necessary for worker health and community relations (permits!). | Avoids shutdowns by regulators, keeps lungs clean, prevents visibility hazards. |
Finding Rock You Can Trust: Supplier Savvy
Buyingcrushed tuff isn’t like buying lumber. Consistency is everything. Here’s how to avoid a nightmare load:
- Reputation is Gold: Ask contractors: “Who supplies the big concrete plants or highway crews?” Suppliers serving picky buyers usually deliver rock-solid consistency. Check reviews specifically for “steady quality” mentions.
- Test Reports or Walk Away: Demandcurrent lab reports (under 6 months old!) for your exact material. Verify these key specs:
- Size Sorting (Sieve Test):
- Must match ASTM C33 (Konkreet) / ASTM D2940 (Road Base) / YOUR project specs
- Red flags: Too much dust (“crusher fines”) or missing middle sizes
- Water Soak-Up (Absorption):
- Tuff drinks 5-15% water vs. granite’s 1-2%
- Critical for concrete: More water needed = weaker concrete if not fixed
- Toughness Rating (LA Abrasion):
- Under 40% = Good for roads
- Under 30% = Premium grade
- Oor 45%? May crumble under trucks
- Weight Density (Specific Gravity):
- Tuff: 1.6-2.0 | Graniet: 2.6-2.8
- Impacts tons-to-yards calculations
- Weathering Test (Soundness):
- Must survive freeze/thaw or wet/dry cycles
- Poor rating = early breakdown in harsh climates
- Size Sorting (Sieve Test):
- Get Your Boots Dirty: Visit the quarryunannounced if possible. See the raw rock faces. Is it consistent color/texture? Watch the crushing operation. Is the screen plant blinding? How are stockpiles managed (segregation is a killer)? Talk to the loader operator – they know the rock’s quirks. Trust your gut.
- Consistency is King: Ask the supplierhow they ensure consistency. Do they blend from different faces? Use sophisticated controls? Or just hope for the best? One bad batch in a concrete pour can cost you six figures.
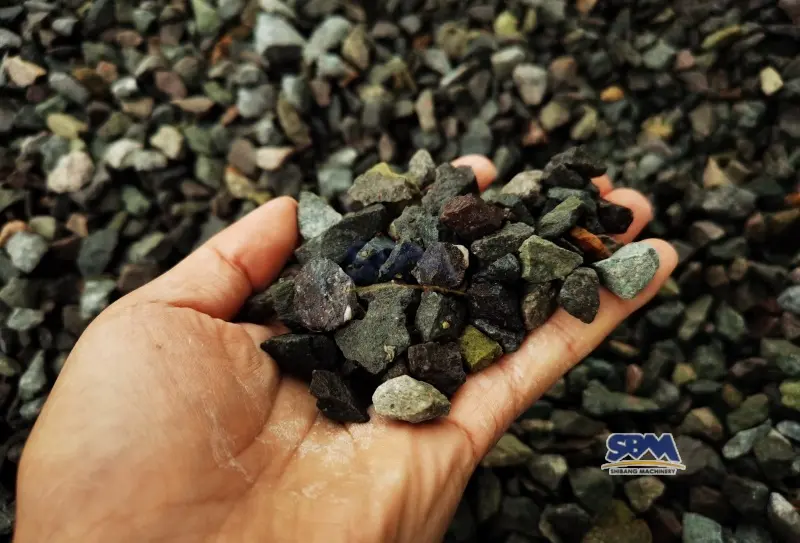
The Bottom Line: Why Crushed Tuff Makes Cents
Let’s talk dollars, not just dirt:
- Freight is the Killer: Hauling 100 tons of traditional aggregate 100 miles? Brutal.Crushed tuff’s lower density means you get morecubic yards per ton. Fewer truckloads = drastically lower freight costs. On remote jobs, this is the make-or-break factor. Fuel surcharges eat less of your lunch.
- Processing Efficiency: Softer rock generally means lower wear part costs and less power consumed per ton crushed. Thiscan translate to a lower price per ton at the pile, depending on the quarry’s efficiency. Negotiate based on volume and consistency.
- Downstream Savings: Lightweight fill means smaller, cheaper retaining walls. Lightweight concrete means reduced structural costs (steel, foundations). These aren’t hypotheticals – they show up clearly in the project bid sheets. Value engineering that actually works.
- Versatility Pays: One stockpile serving multiple needs (drain stone, backfill, decorative top) simplifies ordering, reduces minimum load fees, and minimizes leftover waste. Less hassle, less cost.
- The Local Edge: Using nearbyvolcanic aggregate supports the regional economy. That quarry owner is more likely to cut you a deal on the next big job if you’re a loyal customer. Good relationships matter.
War Stories: Crushed Tuff in the Trenches
- The Sinking Warehouse (Oregon):
- Problem: Cracking floors from uneven settling on soft river soil.
- Regmaak: Dug out 4 feet across whole area → filled with 3 feet of packedcrushed tuff (chosen for lightness + drainage) → new concrete slabs.
- Resultaat: Ground stabilized in months.
- Koste bereken: Hoog, but far cheaper than demolition.
- Secret: Tuff worked like a giant shock-absorbing sponge.
- The High-Rise Core (Mexico City):
- Challenge: Building tall on soft, shaky ground where weight = risk.
- Engineer’s Order: Lightweight concrete for all upper floors/walls.
- Oplossing: Localfyngemaakte vulkaniese rots in concrete mixes:
- Reduced concrete weight
- Lowered earthquake forces on structure
- Avoided imported material delays
Outcome: Pricier than regular rock, but made the tower buildableen safer.
- The Desert Oasis Landscape (Arizona): Client wanted lushlooking but zero-irrigation landscaping. Oplossing? Extensive use of different sizes and colors ofcrushed tuff:
- 3/4″ rusty brown for dry “arroyo” beds.
- 3/8″ creamy gold for meandering paths.
- 1/4″ fines (“tuff sand”) as groundcover around native desert plants.
- Large 8-12″ tuff boulders as focal points.
Rainwater infiltrates instantly, the colors complement the desert palette, and weeds are minimal. Onderhoud? Almost zero. Client satisfaction? Sky-high. Photos went viral locally.
The Flip Side: Challenges & How to Wrestle Them
Crushed tuff isn’t fairy dust. Be ready for:
- The Variability Monster: Tuff from Quarry A ≠ Tuff from Quarry B. Hell, tuff fromFace 3 at Quarry A might differ fromFace 5. Rigorous testing andnot assuming are crucial. Build relationships with suppliers who understand consistency. Get a samplefrom your actual load before it hits the site.
- Dust – The Constant Foe: Drytuff fines are talcum-powder fine and love to fly. During crushing, loading, trucking, placement – it’s pervasive. Mitigation:
- Quarry: Demand effective water sprays at crusher exits, transfer points, and loaders. Enclosed conveyors help.
- Transport: Covered trucks mandatory. Tarp it tight.
- Site: Water down stockpiles liberally before loading. Use water trucks during placement (especially compaction). Respirators for crew aren’t optional PPE. Neighbors will complain if you don’t manage it.
- Absorption Headaches (Konkreet): That thirstyvolcanic aggregate sucks mix water like unbelievable. Pour it dry into the mixer? Disaster. Oplossings:
- Pre-wetting: The gold standard. Stockpile aggregate, saturate it days before batching (keep it covered). Let it reach SSD (Saturated Surface Dry) condition. Requires planning.
- Mix Design Adjustment: Account for absorption in the water/cement ratio. Experienced concrete labs familiar with lightweight aggregate are essential. Don’t wing it. Trial batches are non-negotiable. The extra effort prevents weak, crumbly concrete.
- Friability Fights: Some tuffs simply break down easier under relentless pounding (like unbound high-traffic roads). Know your rock’s LA Abrasion value. If it’s high (above 40%), avoid using it in applications demanding high abrasion resistance. Use it where its drainage or lightness shines instead.
The Horizon: Where Volcanic Aggregate is Headed
This isn’t a fad. The drivers are real:
- Carbon Crunch Intensifies: Regulations and client demands for lower embodied carbon materials will keep rising. Locally sourcedtuff aggregate with its lower transport and processing footprint is perfectly positioned. LEED points will follow.
- Building on the Edge: As prime flat land vanishes, we build on slopes, floodplains, and weak soils.Lightweight fill like crushed tuff becomes essential, not optional. Its stability and drainage are unmatched at its weight.
- Tech in the Quarry: Smarter crushers with automation adjusting settings in real-time for optimal yield and shape. Better dust suppression tech. Drones for stockpile volume management. Efficiency keeps improving.
- Beyond Concrete: Research into using ultrafinepulverized volcanic rock as a supplementary cementitious material (like fly ash) or in geopolymer binders is heating up. Turning quarry “waste” fines into a valuable cement replacement? That’s the holy grail.
Building Smarter with Volcanic Grit
Voorkoms, I’ve poured concrete over river rock, kalksteen, and slag. I’ve packed down enough road base to cover a small state. Crushed tuff isn’t the fix for every job. But when weight, drainage, or going green are key? It stops being just another option—it becomes the clear winner. It asks for care: test it, know it soaks up water, control the dust. But get it right, and it performs where heavier, denser rocks fall short. It’s smart building—using what the local ground offers well. That Sedona crew boss? He now requires crushed tuff for every sloped drainage job. Watching a doubter become a believer? That says it all. Skip the plain gravel now and then. Try volcanic rock. Your building’s base—and likely your bottom line—will be grateful.