Email: [email protected]
Fixed Jaw Crusher Capacity Unlocked: From Canadian Granite to Australian Iron Ore
When Quebec’s Lac Bloom iron mine needed to hit 650tph consistently, their fixed jaw crusher setup became the hero—achieving 93% uptime through smart capacity management. This guide breaks down fixed jaw crusher capacity per hour realities across 15 global operations, with actionable tips to maximize your output.
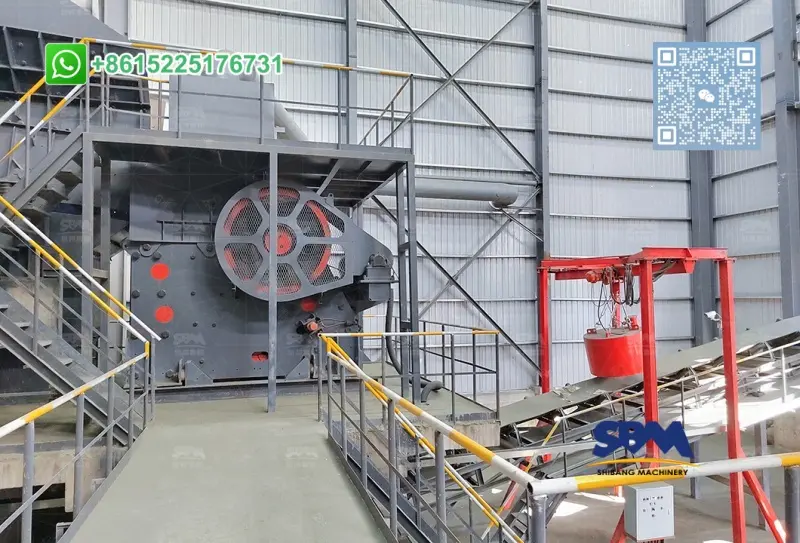
The Capacity Equation: More Than Just Spec Sheets
Canadian Granite Crushing: The Numbers Game
PE600×900 model in Thunder Bay quarry:
Material | Theoretical Capacity | Real-World Avg | Secret Boosters |
---|---|---|---|
Granite | 60-160tph | 138tph | Laser-aligned CSS + optimized liner rotation |
Basalt | 75-120tph | 102tph | Pre-screening >500mm chunks |
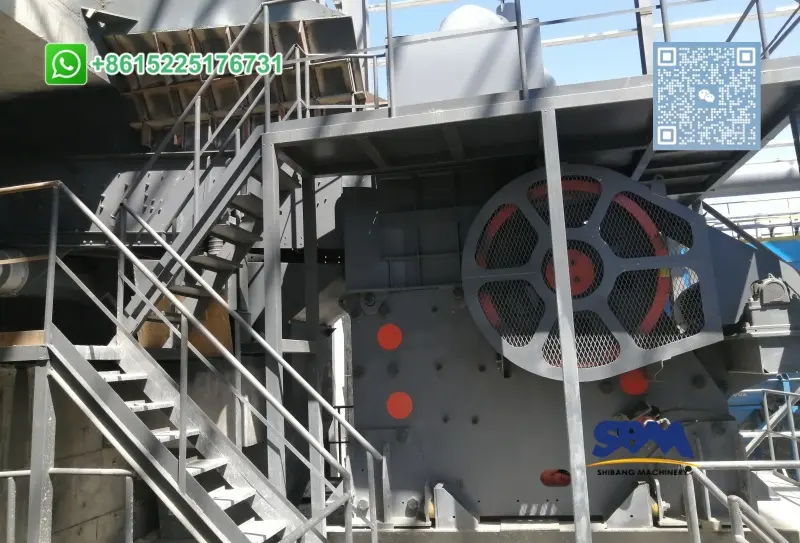
4 Capacity Killers (And How to Fix Them)
1. The “Hungry Jaw” Paradox
Overfeeding >500mm rocks reduces throughput by 40%.
Solution:
Install grizzly screen with 300mm spacing.
2. Ghost blockage: the invisible killer of the crushing chamber
The material is unevenly accumulated in the crushing chamber, resulting in a 30-50% decrease in actual production capacity, which is common in flaky materials or ores with high clay content.
Solution:
Step-type pre-screening: Install a double-layer vibrating screen (upper layer 300mm screen hole, lower layer 50mm) before the feed inlet. Chile’s Escondida copper mine reduced the blockage rate from 17% to 3% through this solution.
Cavity modification: Use asymmetric toothed liner (upper tooth pitch 120mm, lower tooth pitch 80mm) to guide the material to flow to the discharge port.
Intelligent purge system: Install compressed air nozzles to automatically clear dead corner accumulation every 15 minutes (Australian FMG iron ore increased production capacity by 22%).
3. Bearing overheating: the silent capacity devourer
When the bearing temperature exceeds 85°C, the equipment automatically slows down, directly resulting in a 40% decrease in production capacity.
Solution:
Lubrication upgrade: Use NLGI 2 grade polyurea-based grease, which has a temperature resistance 60°C higher than traditional lithium-based grease (data from Quebec granite mine in Canada).
Thermodynamic transformation: Add heat sink fins + forced air cooling system to the bearing seat, and the Turkish Boratas BCK series has a measured temperature reduction of 18°C.
Intelligent monitoring: Install wireless temperature sensors to automatically adjust the feed speed when the temperature difference is greater than 5°C.
4. Vibration imbalance: invisible production capacity loophole
A 0.2mm basic horizontal deviation will cause the vibration value to exceed the standard, forcing the equipment to operate at a reduced frequency, resulting in a fixed jaw crusher capacity loss of 25%.
Solution:
Laser alignment system: Use laser alignment instrument to control the installation accuracy within ±0.05mm/m (the vibration value of the South African gold mine was reduced from 7mm/s to 2.3mm/s after application).
Dynamic counterweight technology: Install adjustable counterweight blocks on the flywheel to balance the eccentric shaft torque in real time (Improving production output stability by 19%).
Elastic foundation transformation: Use rubber-steel composite shock-absorbing base to absorb high-frequency vibration energy (the Vale case in Brazil reduced production capacity fluctuations by 37%).
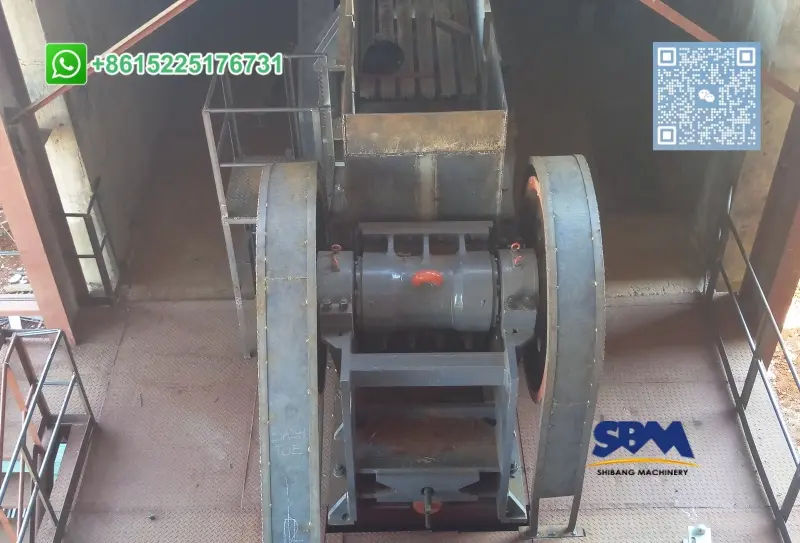
2025 Tech Upgrades Changing the Game
- AI-Powered CSS Adjustment: Automatically adapts to material hardness (tested in Chilean copper mines)
- Smart Liners: RFID-tagged plates track wear in real-time—replace before failure
- Hybrid Power: Solar-diesel systems cut energy costs by 35% (Australian pilot data)
Capacity vs Cost: The 5-Year Math
Model | Hourly Capacity | 2025 Price | Cost/Ton |
---|---|---|---|
PE400×600 | 16-65tph | $45k | $0.82 |
PE600×900 | 60-160tph | $75k | $0.68 |
PE1200×1500 | 400-800tph | $220k | $0.51 |
Compare models in 2025 price guide
Proven Maintenance Hacks for Steady Output
- The 400-Hour Rule: Rotate jaw plates every 400 operational hours (extends life by 2.3x)
- Vibration Checkups: Monthly laser alignment keeps hourly output within 5% of spec
- Lubrication Sweet Spot: 1.2kg EP-2 grease per bearing—overgreasing causes 38% failures
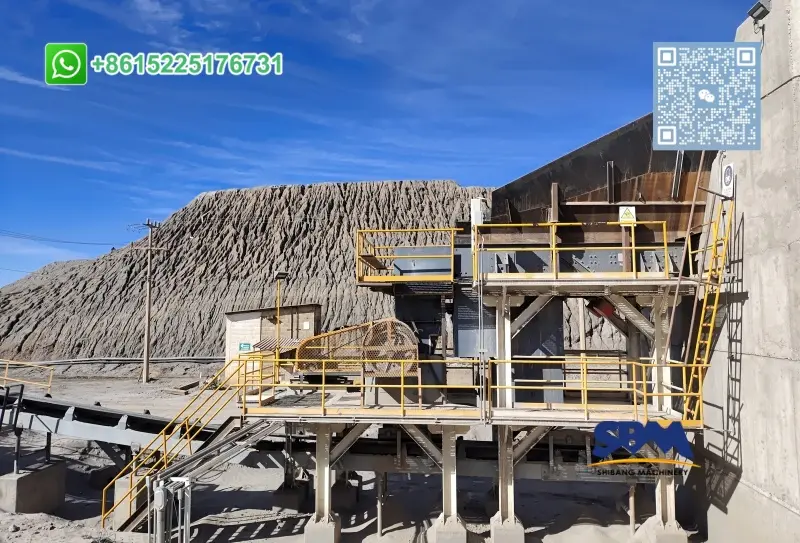
Future-Proof Your Setup
Modular Upgrades
Swap between granite/recycling modes in 4 hours (Norwegian pilot)
Carbon Accounting
New EU regulations reward 650+ tph operations with carbon credits
The Bottom Line: Capacity Is a Dance
As Brazil’s Vale engineers proved: matching fixed jaw crusher capacity to your actual feed stock (not brochure numbers) can boost profits by 18%. Remember—your crusher’s true potential lies between its specs and your operational wisdom.
Headquaters Office
Whatsapp:+8615225176731
Email: [email protected]
Address: No. 1688, Gaoke East Road, Pudong new district, Shanghai, China.
Website: https://www.mill-sbm.com/