Email: [email protected]
Step-by-Step Guide to Replacing Jaw Crusher Liners: 8 Key Phases
Properly replacing jaw crusher liner increases production efficiency by 40% and extends component life by 2-3 years. This comprehensive guide details professional techniques used in small and large mining operations, covering safety protocols, tool requirements, and precision alignment methods. Follow our 8-phase process to minimize downtime to under 4 hours per replacement.
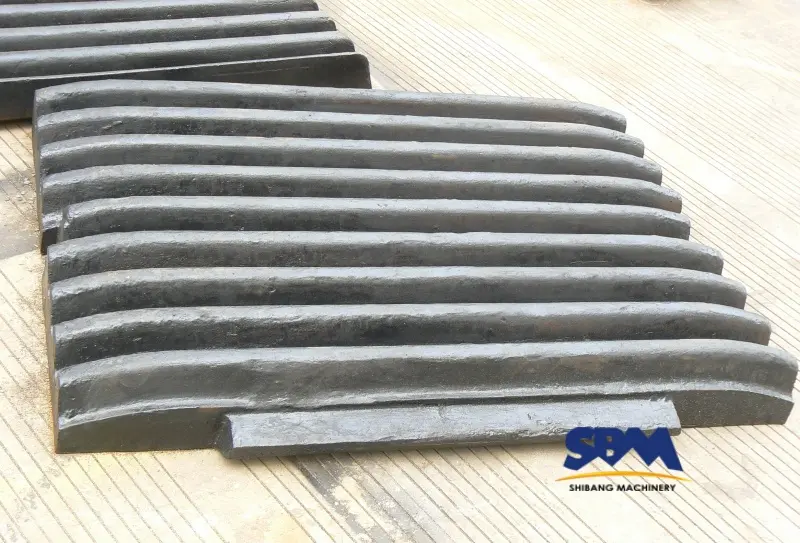
Pre-Replacement Preparation
1. Safety Lockout Procedure
- Disconnect power supply and engage mechanical lockout
- Release hydraulic pressure (>5 minutes bleed time)
- Install fall protection for crusher pit access
2. Tool & Material Checklist
Tool | Specification |
---|---|
Hydraulic Jack | 50-ton capacity |
Torque Wrench | 300-800 N·m range |
Liner Lifting Clamp | SWL 2,000kg |
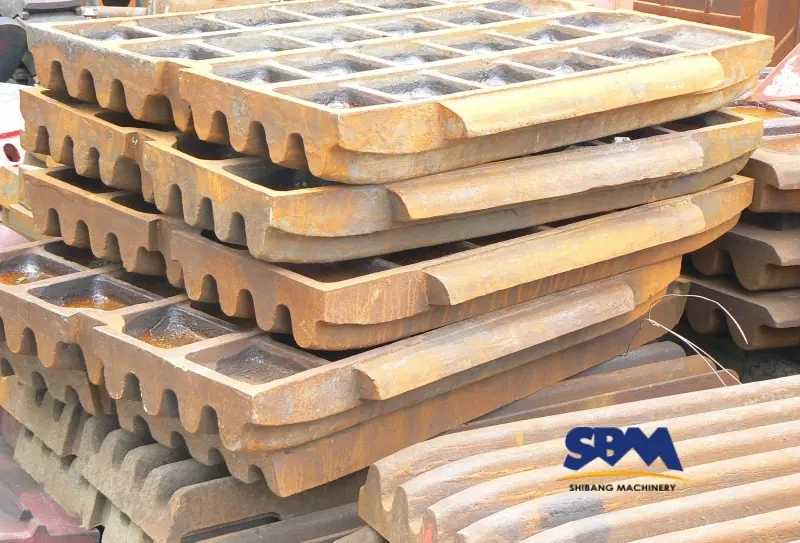
Liner Replacement Process
3. Remove Worn Liners
- Loosen wedge bolts in diagonal pattern (30% torque reduction)
- Use liner removal tools to break corrosion bond
- Extract upper wedges first, then side plates
4. Clean & Inspect Mounting Surface
- Remove debris with pneumatic chisel
- Check for cracks using dye penetrant
- Verify flatness (<0.5mm/m tolerance)
5. Install New Liners
Component | Torque Spec | Sequence |
---|---|---|
Fixed Jaw | 650 N·m | Center-out |
Movable Jaw | 720 N·m | Cross pattern |
6. Alignment Verification
Use laser alignment tools to ensure:
- Parallelism <0.2mm/m
- Vertical runout <0.3mm
- Proper crushing chamber geometry
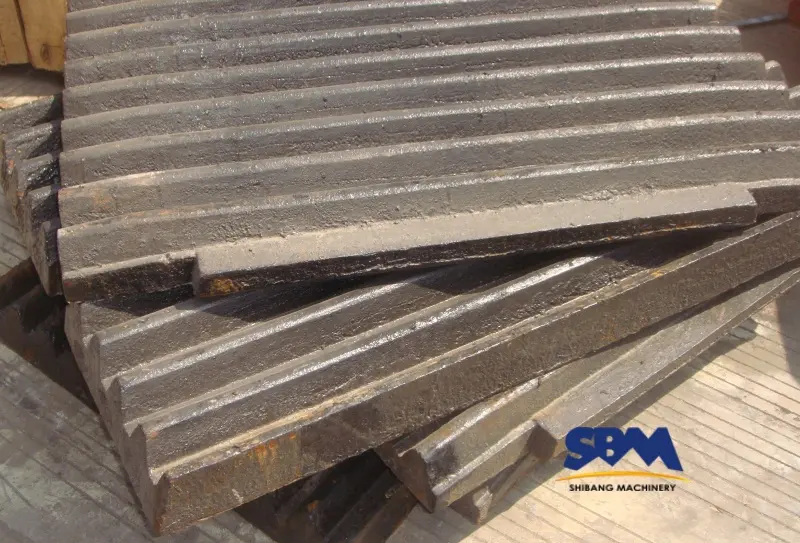
Post-Installation Procedures
7. Run-in Process
- Start with 50% feed rate for 2 hours
- Monitor vibration (<4.5 mm/s RMS)
- Retorque after 8 hours operation
8. Documentation & Analysis
- Record liner serial numbers
- Measure initial wear pattern
- Update predictive maintenance schedule
Common Mistakes & Solutions
Error | Consequence | Prevention |
---|---|---|
Improper torque | Liner movement | Use calibrated wrench |
Missed alignment | Premature wear | Laser verification |
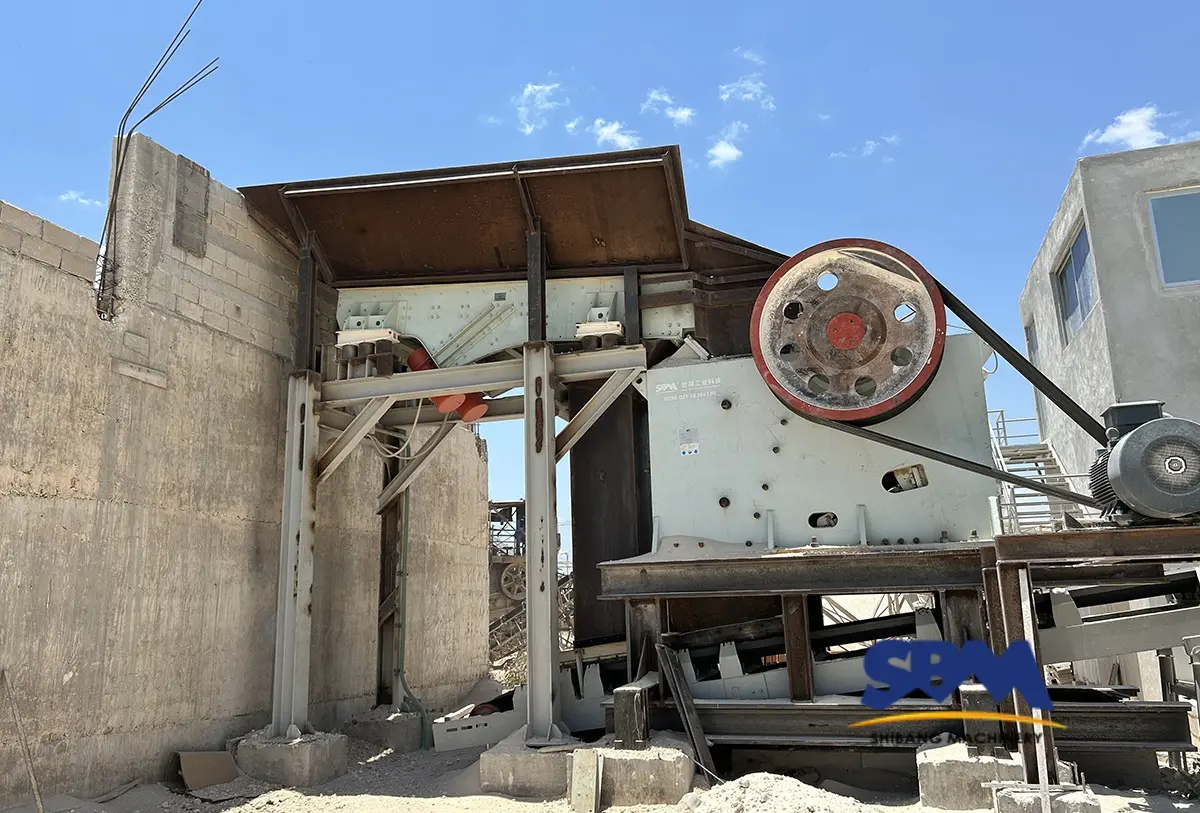
Quarry Productivity Improvement
A limestone operation reduced liner replacement time from 6.5 to 3.8 hours by:
- Implementing our 8-step process
- Using optimized liner profiles
- Training crew on crusher kinematics
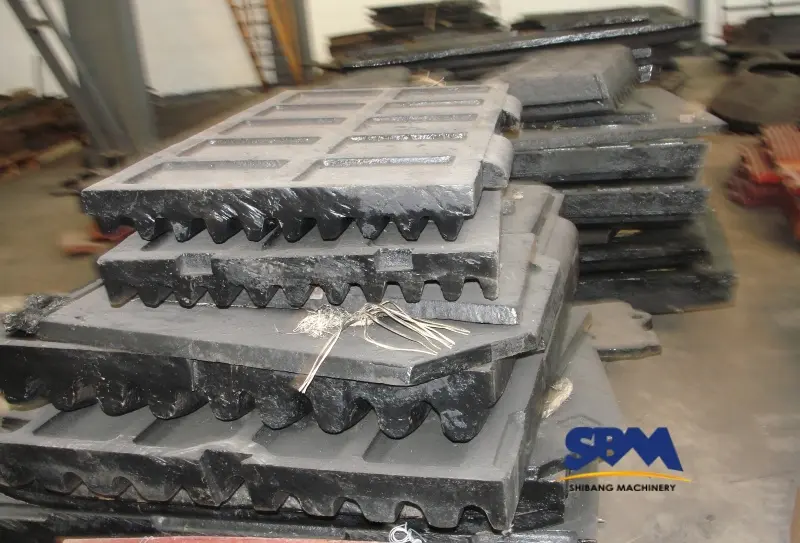
Essential Tools for Efficient Replacement
- Liner handler with vacuum lift
- Infrared thermal camera (check bearing temps)
- Digital thickness gauge (wear measurement)
Precision Saves Costs
Replacing jaw crusher liner requires understanding torque specifications, alignment tolerances, and proper run-in procedures. Therefore, by integrating this guide with your preventive maintenance program and equipment documentation, operations typically achieve 18-24 month liner lifecycles even in abrasive conditions.
Headquaters Office
Whatsapp:+8615225176731
Email: [email protected]
Address: No. 1688, Gaoke East Road, Pudong new district, Shanghai, China.
Website: https://www.mill-sbm.com/