Email: [email protected]
Common Jaw Crusher Problems and Solutions: Your Complete Maintenance Checklist
Over 65% of unplanned downtime in jaw crusher operations stems from preventable mechanical issues. This comprehensive guide identifies the 7 most common jaw crusher problems and provides actionable solutions, complete with a maintenance checklist to keep your C6X Jaw Crusher or other models running optimally.
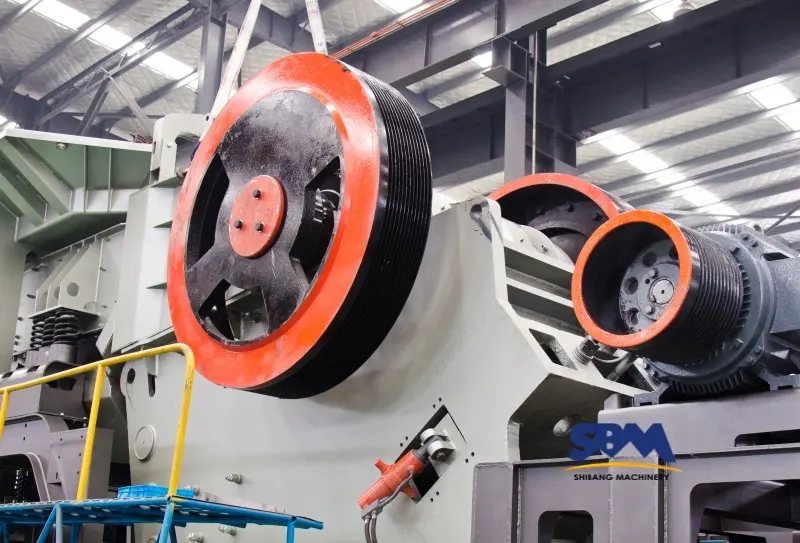
Top 7 Jaw Crusher Issues & Immediate Fixes
1. Uneven Jaw Plate Wear
Symptoms: 30-50% faster wear on one side
Solutions:
- Rotate plates every 200 operating hours
- Check feed distribution with laser alignment
- Upgrade to asymmetric tooth profiles for mixed materials
2. Excessive Vibration
Symptoms: Structural shaking >5mm/s RMS
Root Cause:
- Worn bearings (85% of cases)
- Unbalanced flywheel (12%)
- Loose foundation bolts (3%)
Fix:
- Torque all bolts to 350 N·m specification
- Replace tapered roller bearings using proper installation techniques
3. Low Production Output
Symptoms: Throughput drops >20%
Diagnosis:
Possible Causes | Verification Method | Solution |
---|---|---|
Worn jaw dies | Measure plate thickness | Replace at 60% wear limit |
Incorrect CSS setting | Laser measurement | Adjust to OEM specifications |
Material bridging | Visual inspection | Install grizzly feeder |
4. Hydraulic System Overheating
Symptoms: Oil temperature >80°C
Solutions:
- Clean clogged radiator fins weekly
- Replace hydraulic filters every 500 hours
- Upgrade to synthetic high-temp oil (ISO VG 68)
5. Abnormal Noise During Operation
Sound Types & Meanings:
- Metallic grinding: Worn toggle seats
- Loud banging: Broken toggle plate
- High-pitched squeal: Dry bearings
Action Plan:
- Immediately stop operation
- Inspect components using diagnostic checklist
- Replace damaged parts before restarting
6. Frequent Bearing Failures
Prevention Strategy:
- Use laser alignment for perfect shaft positioning (±0.05mm)
- Implement automatic lubrication systems
- Monitor temperature with wireless IoT sensors
7. Oil Contamination Issues
Contamination Sources:
Contaminant | Max Allowable | Removal Method |
---|---|---|
Dirt particles | ISO 16/13 | Centrifugal filters |
Water | 0.1% volume | Vacuum dehydration |
Metallic debris | >50μm | Magnetic plugs |
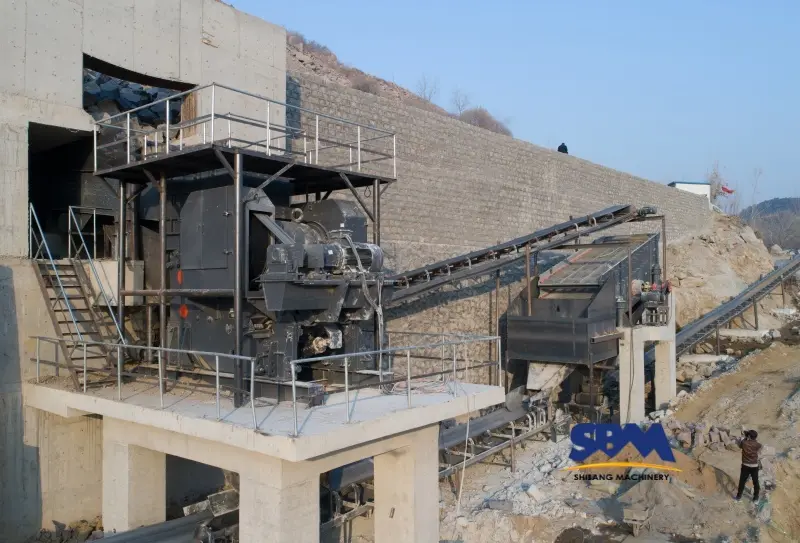
Proactive Maintenance Checklist
Daily Tasks
- Check oil levels and contamination (use patch test)
- Inspect belt tension (deflection <15mm)
Weekly Actions
- Measure CSS with laser gauge
- Test safety interlocks
Monthly Priorities
- Perform vibration analysis (2-5mm/s limit)
- Inspect structural welds for cracks
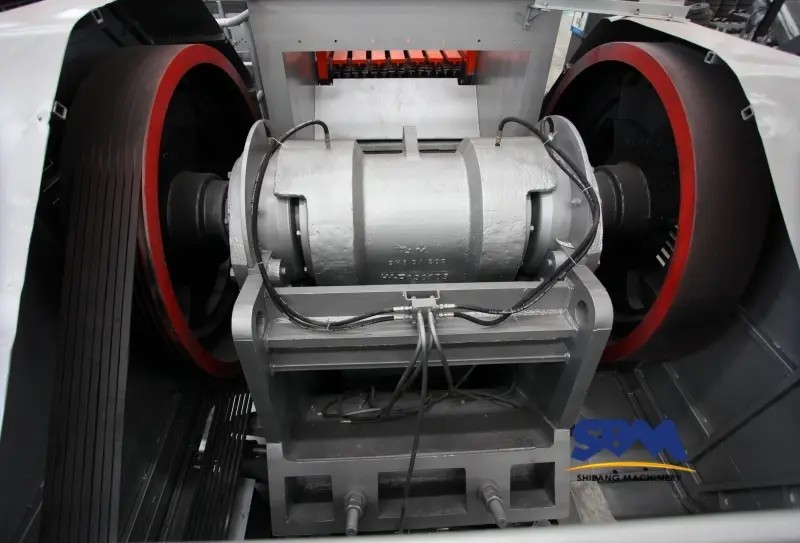
Critical Component Failure Prevention
Toggle Plate Breakage
Early Warning Signs:
- Output size variation >15%
- Unusual clicking during crushing cycles
Prevention: Replace after 800-1200 hours in abrasive conditions
Advanced Monitoring Techniques
- Infrared thermography for bearing health checks
- Vibration analysis (2-5 mm/s RMS threshold)
- Oil debris sensors detecting >50μm particles
When to Seek Professional Help
Contact OEM technicians if experiencing:
- Persistent capacity drops >25% after routine maintenance
- Frame cracks exceeding 2mm width
- Eccentric shaft runout >0.15mm
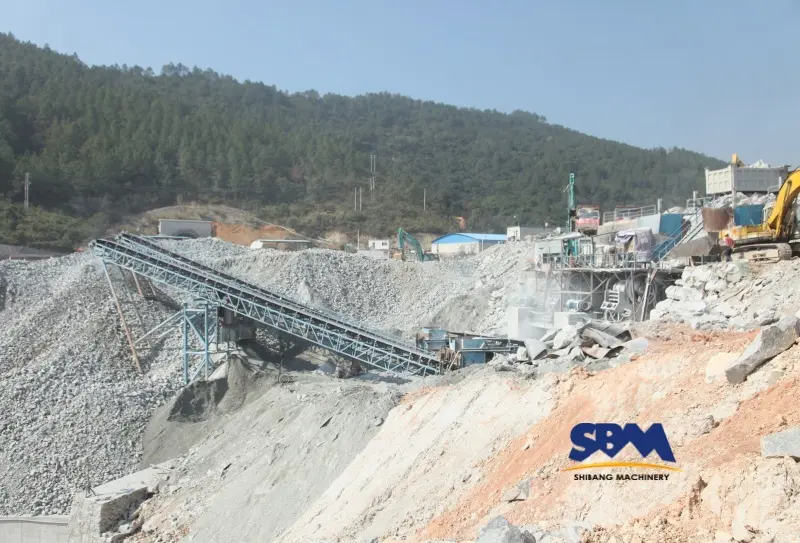
Case Study: Solving Chronic Overheating
A limestone quarry reduced bearing failures by 70% through:
- Upgrading to synthetic high-temp grease
- Installing automatic lubrication systems
- Implementing our monthly inspection protocol
Essential Tools for Effective Maintenance
- Laser alignment kit (±0.1mm accuracy)
- Digital torque wrench (50-500 N·m range)
- Wear measurement calipers
Systematic Prevention Wins
By addressing these common jaw crusher problems through our maintenance checklist, operators achieve >92% uptime. Also, remember: 80% of failures originate from just 20% of components – focus on bearings, jaw plates, and hydraulic systems. Finally, pair this guide with proper operation training for maximum equipment lifespan.
Headquaters Office
Whatsapp:+8615225176731
Email: [email protected]
Address: No. 1688, Gaoke East Road, Pudong new district, Shanghai, China.
Website: https://www.mill-sbm.com/