Email: [email protected]
What is Limestone Grinding Mill
A limestone grinding mill is a machine that grinds and powderizes limestone. It is very useful in the manufacture of cement, glass, steel and other industrial products that require finely ground limestone. Limestone enters the mill where it is processed and crushed by grinding media (balls or rollers). Separators collect the resulting powders, which are often raw materials or additives in various industries. Limestone grinding mills come in a variety of sizes and designs, but they always have a spinning cylinder or bowl with grinding medium and an internal classifier or separator to regulate the particle size distribution of the ground limestone.
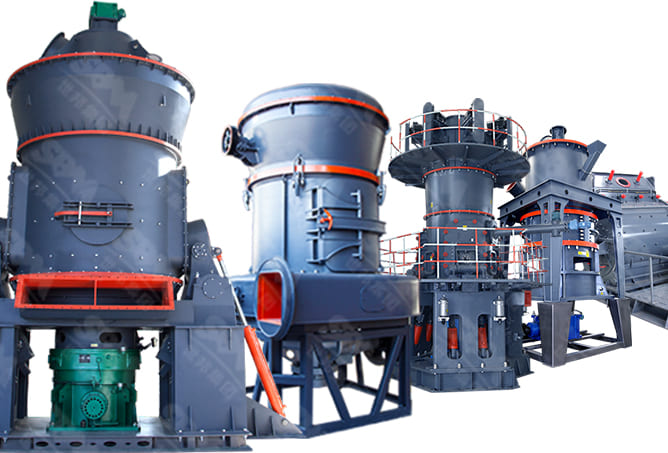
The Different Types of Limestone Grinding Mills Available
There are several different types of limestone grinding mills available, each designed for specific purposes and applications.
Raymond Mill
This mill, also known as the Raymond Roller Mill, is a common choice for limestone grinding. It works by rotating a grinding ring or roller around a fixed shaft, allowing the material to be ground by the rolling and crushing action between the grinding parts.
Ball Mill
A ball mill is a cylindrical device used to finely grind materials. It consists of a horizontally rotating drum. Grinding media such as steel balls are installed in the drum. These grinding media impact and grind the limestone as the drum rotates.

Vertical Roller Mill (VRM)
This mill grinds and separates the limestone into different particle sizes using several rollers. When compared to other types of mills, it delivers effective grinding with a smaller footprint.
High Pressure Grinding Mill
This mill, also known as an HPGR mill, uses high pressure to the material being ground, resulting in finer particle size reduction. We use it widely for limestone grinding in mining industry.

Ultrafine Mill
This mill typically performs ultra-fine grinding of friable minerals such as limestone. It impacts and pulverizes the material using centrifugal force to produce very small particle sizes.
Hammer Mill
A hammer mill can also crush limestone into smaller pieces, although its primary purpose is crushing. It operates by quickly revolving hammers striking the material and shattering it into smaller pieces inside a chamber.
These are only a few illustrations of the various kinds of limestone grinding mills that are accessible. The preferred particle size, required capacity, energy efficiency, and the unique properties of the limestone being processed are all important considerations in choosing the right mill.
What factors should be considered when purchasing a limestone grinding mill?
When purchasing a limestone grinding machine, we should consider several important factors to ensure the best performance and value for our particular application. Here are some of the key factors to consider:
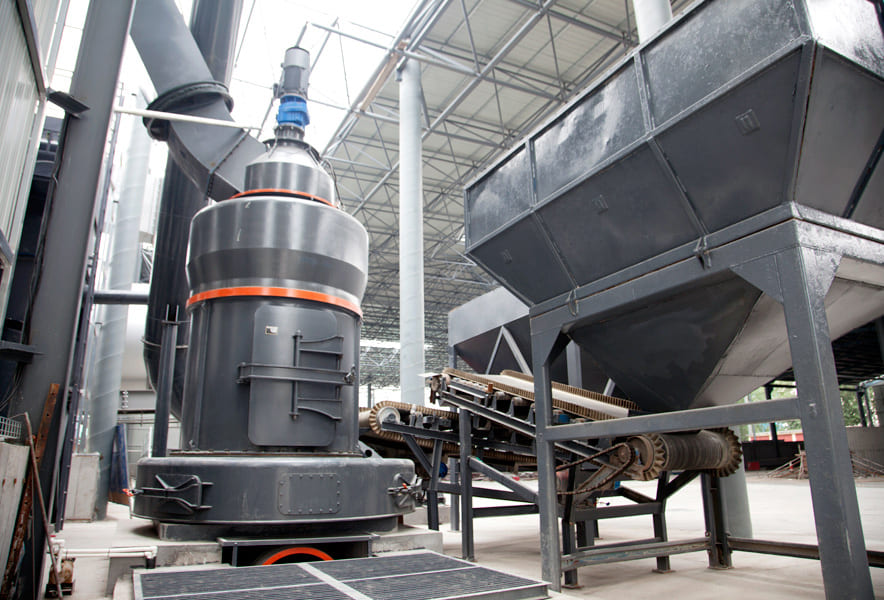
Capacity Requirements
The grinding mill’s capacity should correspond to our business’s requirements for output. We have to take into account the amount of limestone to be processed, the expected output and the production rate.
Particle Size Requirements
Particle sizes needed for various industries’ finished goods vary. We should be able to achieve the necessary particle size distribution using the grinding mill we select.
Energy Efficiency
A grinding mill’s energy use represents a considerable running expense, thus choosing one that is energy efficient is crucial. This might save operational expenses and increase sustainability.
Maintenance Requirements
Maintenance costs are another important consideration. Make sure that the replacement parts are easily accessible when choosing a grinding mill, and it should be simple to maintain and repair.
Cost
In addition to long-term operating expenses, we should also consider the initial purchase cost of the mill. Selecting a grinding mill that offers a favorable balance between upfront cost and operational costs is crucial.
Brand Reputation
Choose a reliable company that has a track record of providing grinding mills of the highest caliber. Before making a purchase, look for references, reviews, and testimonies.
Customization Options
Think about a grinding mill that can be altered to match our unique requirements if our application calls for certain features or alterations.
We may choose the ideal limestone grinding mill for our unique application by taking these aspects into account, ensuring that we obtain the optimum performance and return on our investment.
How to optimize the performance and efficiency of a limestone grinding mill?
To optimize the performance and efficiency of a limestone grinding mill, we can consider the following strategies and techniques:
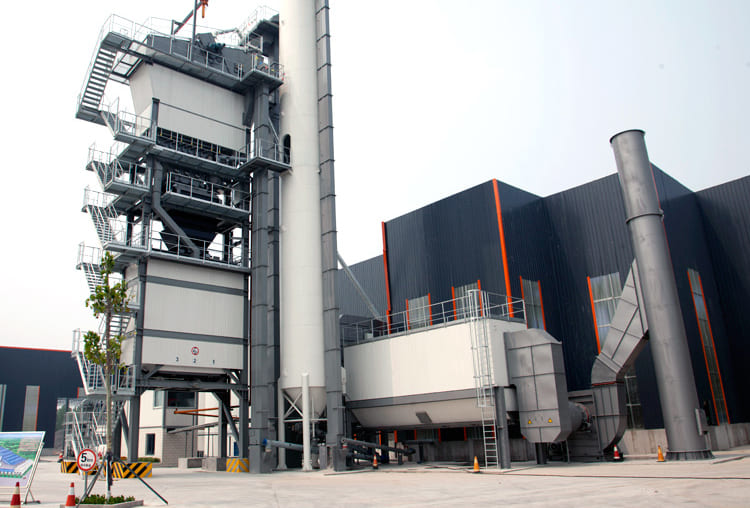
Proper equipment selection
Make sure we have a grinding mill that is the appropriate size and type for processing limestone. Mill type (such as a ball mill, vertical roller mill, or Raymond mill), capacity, power consumption, and overall efficiency are all important factors to take into account.
Optimize mill parameters
To get the best performance out of the mill, modify its operating settings. These variables include the following: mill speed, feed rate, size and distribution of the grinding medium, and grinding pressure. Try out several parameters to find the one that produces the ideal particle size distribution while using the least amount of energy.
Optimize feed size
Size the limestone input to the mill appropriately. Grinding will often be more effective if the feed particles are smaller and more uniform in size. Before putting larger chunks of limestone into the mill, think about utilizing pre-crushing equipment to reduce their size.
Maintain consistent feed rate
Make sure the feed rate into the mill is constant and under control. Changes in feed rate can have an impact on the effectiveness of the grinding process and lead to uneven product quality. To control the flow of limestone into the mill, take into consideration employing feeders or other machinery.
Optimize grinding media
For the mill, pick the right size and kind of grinding media (such as steel balls or ceramic beads). The proper medium will increase grinding effectiveness and lower energy usage. To maintain peak performance, inspect and replace worn-out or damaged media often.
Regular maintenance
Implement a thorough maintenance schedule to keep the mill in excellent working order. This involves routine cleaning to avoid buildup and obstructions that might lower efficiency, examination and repair of worn parts, and lubrication of bearings.
Monitor and control process variables
Use process control systems to track and manage crucial parameters like mill temperature, product fineness, and power usage. We can use this data to improve grinding and identify any issues affecting performance.
Consider automation
To improve the functioning of the mill, implement automation and cutting-edge control technologies. Based on data from sensors and analytical tools, these systems may modify mill settings in real-time, improving consistency and efficiency.
Energy efficiency measures
Use energy-saving techniques including high-efficiency motors, better air flow and ventilation, and less unneeded mill shutdowns. By reducing energy usage, there will be an overall increase in the efficiency of the grinding process.
Continuous improvement and optimization
Examine the grinding mill’s functioning on a regular basis and note any shortcomings. Conduct routine audits, examine data, and compare results to industry norms to encourage ongoing optimization and reach greater levels of effectiveness and performance.
Keep in mind that the particular improvements will differ based on the kind and design of the grinding mill we are using. For more detailed advice customized to our equipment and operating needs, talk with the mill manufacturer or process specialists.
Headquaters Office
Whatsapp:+8615225176731
Email: [email protected]
Address: No. 1688, Gaoke East Road, Pudong new district, Shanghai, China.
Website: https://www.mill-sbm.com/