Email: [email protected]
What is pebble crushing?
Let’s talk rocks. Not just any rocks, but those stubborn, smooth, incredibly hard nuggets nature polishes in riverbeds – pebbles. If you’re running a mill or an aggregate plant, you know these guys. They recirculate, they wear down gear, they bottleneck your flow. What is pebble crushing? It’s not some abstract concept; it’s the daily grind (literally) of wresting value from the toughest stones nature throws at us. Forget sterile definitions. Pebble crushing is survival and profit in the mineral processing and aggregate game. It’s the specialized art of breaking down hard, rounded river stones or tough “critical size” chunks recirculating in your SAG mill, turning a headache into a payday. I’ve stood on those vibrating platforms, felt the rumble of the crusher, and seen the relief on an operator’s face when the circuit finally hums. That’s what this is about.
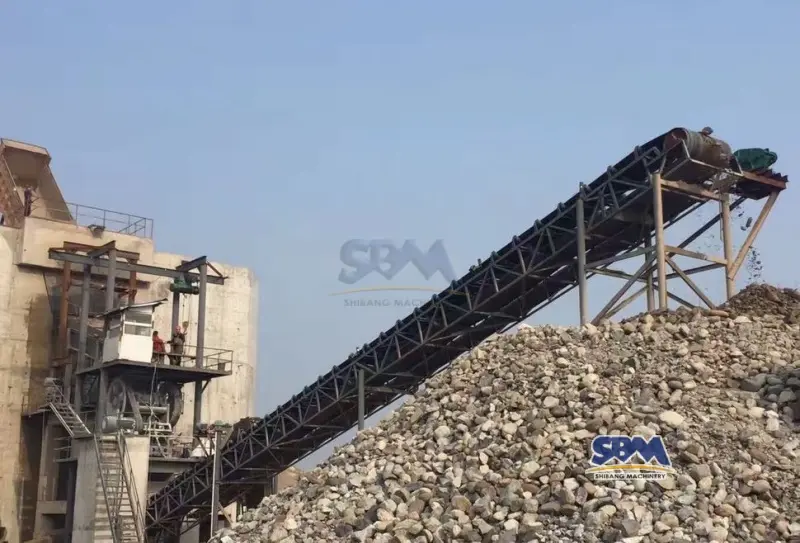
Why Pebbles Keep Plant Managers Up at Night (And Why Crushing Them is the Cure)?
Let’s be real: Pebbles aren’t evil, but their natural traits make them a major headache:
- Harder Than a Bad Week: River quartzite? It wears out soft steel fast. This hardness means rapid wear on any equipment touching it.
- Slick and Uncooperative: That beautiful, smooth, rounded shape? Terrible for crushing! They slide, they roll, they resist getting a good grip. Angular feed is predictable; pebbles are like trying to crush marbles.
- Circuit Cloggers Extraordinaire: Especially in SAG/AG mills. They don’t grind down easily, so they just keep circulating, building up volume, stealing energy, and dragging your entire throughput down. It’s like paying to run a mill full of ball bearings.
- Wasted Gold (Literally Sometimes): That recirculating load? It’s valuable ore not being processed well. Natural river pebbles? Top-grade construction material going unused.
Ignoring efficient cobble crushing isn’t an option. It’s signing up for higher power bills, constant liner changes, frustrating bottlenecks, and leaving money on the table – or in the riverbed.
Getting Down to Brass Tacks: How We Actually Crush These Things?
The process of crushing pebbles isn’t magic, but it demands respect and the right approach. Here’s the gritty reality:
1. Where the Trouble Starts (The Feed)
Pebbles typically enter the system from:
- SAG/AG Mill Recirculation: The main source. Oversize pebbles screened from mill discharge need size reduction before returning to the circuit. These are “critical size” pebbles.
- Natural Sources: Riverbeds & gravel pits feeding aggregate plants. Tough material that’s hard on equipment.
- Quarry Operations: Hard rock crushing sometimes produces pebble-sized material needing further processing.
2. Managing the Flow (Feeding & Screening)
Never dump pebbles straight into the crusher. Essential equipment:
- Heavy-duty feeders for steady material flow
- Scalping screens before crushing to remove fines – critical for protecting your crusher
3. The Main Event: The Crush
This is where the muscle meets the stone. Forget jaw crushers or impacts for primary pebble duty; they’ll get chewed up. Pebble crushers need to apply immense, focused force – primarily compression. That’s why cone crushers rule this roost. They squeeze those stubborn rocks between a mantle and concave liner, often forcing them to break each other. It’s brutal, effective, and requires serious engineering. I’ve seen poorly set crushers scream and shudder under this load – it’s not a sound you forget.
4. Moving the Goods (Product Handling)
Once tamed, the crushed product needs to go somewhere. Robust conveyors (think heavy belts, good sealing – dust is a beast) carry it either back to the mill circuit, to secondary grinding (like a ball mill), or straight to sizing screens and stockpiles for aggregate. No room for flimsy gear here; the abrasiveness hasn’t magically disappeared.
The Unsung Heroes: Pebble Crushers Built for Battle
Not all crushers are built the same. Handling tough river gravel needs battle-tested machines. Cone crushers lead the pack, and here’s why they deliver:
- Compression is King: Breaking hard, abrasive rock? Squeezing force works best. Cone crushers master this method.
- Smart “Rock-on-Rock” Action: The chamber’s shape makes pebbles smash into each other. This slams rocks together, cutting way down on liner wear – a big money saver.
- Adjust While Running: Modern hydraulics let you change the crusher’s gap (Closed-Side Setting – CSS) on the fly. This keeps product size steady as liners wear, with no shutdowns for manual tweaks.
- Built Tough from Top to Bottom: Every part – base to main shaft – soaks up heavy pounding and constant scraping. Anything weaker breaks down fast.
Choosing Your Champion: Cone Crusher Types for Pebble Duty
Feature | Multi-Cylinder Hydraulic Cone Crusher (The Workhorse) | High-Speed Cone Crusher (The Specialist) | Gyratory Crusher (The Heavy Hauler) |
---|---|---|---|
Where It Shines | The go-to for most pebble apps. High capacity, excellent control over product shape, good wear life when spec’d right. Handles SAG recirc and large aggregate plants beautifully. | Delivers finer product sizes and higher reduction ratios in a single pass. Good particle shape. | Handles big volumes for first-stage crushing of large natural pebble deposits. Ideal for major river gravel operations. |
Secret Weapon | Better rock-on-rock crushing from smart chamber design. Hydraulic systems are strong and precise. | Achieves its results through higher rotational speeds. Can be very efficient for specific size targets. | Raw tonnage capability. Can swallow enormous feed. |
Watch Out For… | Liner selection & maintenance are critical. Wrong profile or cheap steel costs you dearly in downtime and consumables. Feed size discipline is non-negotiable. | Can be more sensitive to highly abrasive feeds – liners might wear faster than on a multi-cylinder. Not always the toughest option for constant severe duty. | Takes up lots of space and costs much more. Complicated to install. Far too powerful for normal SAG mill recirculation setups. |
Best Pebble Fit | SAG/AG Mill Recirculation (90%+ of the time!), Large-scale aggregate crushing requiring consistent shape & size. | Smaller recirculation circuits, aggregate plants needing specific fine fractions efficiently. | Primary crushing station for massive natural river gravel or glacial deposit operations. |
Personal Note | “This is our bread and butter. A well-set multi-cylinder, fed right, with good liners? It sings. Get one thing wrong? It screams.” | “Useful tool, but know its limits on wear. Great when you need that extra reduction.” | “Seen them used well on truly epic gravel deposits. For most mines? Like using a sledgehammer to crack a walnut.” |
It Takes More Than Just a Crusher: The Supporting Cast
A pebble crushing plant is an ecosystem. Neglect any part, and the whole thing suffers:
- Feeders: More than simple conveyors. Tough vibrating grizzly feeders (VGFs) or heavy apron feeders are vital for controlling the flow of hard feed and shielding the crusher from sudden rushes. A cone crusher runs best when full; feeders make this happen.
- Screens: Scalping screens act as bodyguards. You need rugged, high-shake screens to take the rough treatment and pull out fine material before crushing. Final sizing screens need equal toughness. Fighting screen wear never stops.
- Conveyors: You’re moving sandpaper-like material. Use belts that resist scraping, strong rollers, and tight seals to trap dust. Cutting corners here means endless spill cleaning and early breakdowns. I’ve wasted hours clearing blockages from conveyors buried under crushed pebble…
- Dust Suppression: Crushing hard rock makes dust. Always. Good dust control (water sprays, fog machines, smart covers) isn’t just about rules; it protects workers’ lungs and stops your whole plant from turning grey. A proper system makes a huge difference.
- The Steel Itself: This is the make-or-break spot. Crusher liners (mantles, bowls, screen panels) MUST be top-grade manganese steel or special hard alloys. The cost gap between cheap and quality liners per ton is massive. It’s not a cost – it’s an investment. Finding liners worn razor-thin way too soon? That’s a pain we help plants avoid.
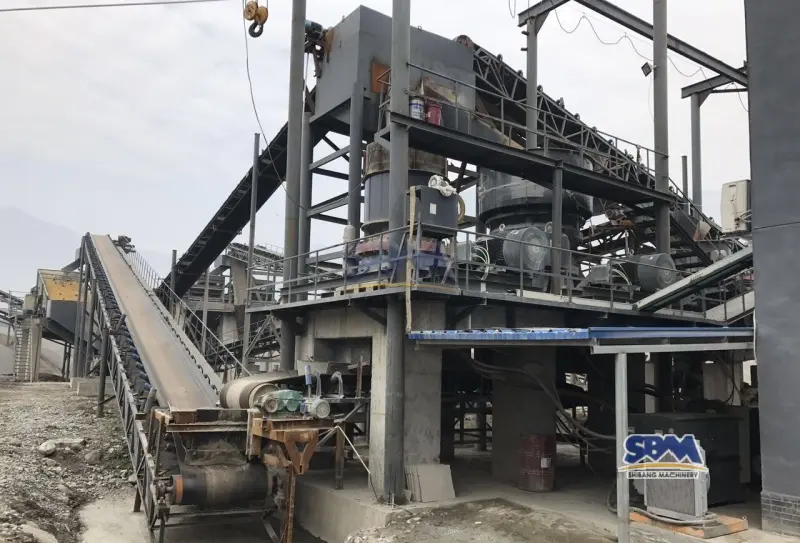
Where the Rubber Meets the Road: Pebble Crushing in Action?
Understanding what pebble crushing is means seeing it solve real problems:
- Mineral Processing: The Heart of the Matter:
- Taming the SAG/AG Mill Beast: This is where pebble crushing shows its value every day. Handling that circulating load of hard-to-grind pebbles isn’t just helpful; it’s essential for squeezing 5%, 10%, or even 15% more tons out of your whole grinding circuit. That means more product shipped. I recall visiting a gold mine battling low output; their pebble crusher was too small and poorly kept. Upgrading it and fine-tuning the liner setup opened the floodgates – the SAG mill ran smoother, power steadied, and production surged. That’s real impact.
- Pebble Milling Power: Sometimes, the crushed pebbles feed special pebble mills – using the stones’ own hardness to grind ore. Good primary crushing is vital here too.
- Aggregate Production: Building the World:
- Concrete That Lasts: Crushed river pebbles make some of the toughest concrete rock mix available. The smoothness is broken, creating perfect rough edges for binding.
- Roads That Endure: From solid road foundations to stable drainage layers to hard-wearing surfaces, crushed pebble gravel is key infrastructure material. Nothing beats its strength and longevity.
- Keeping Trains on Track: Train tracks need rough, interlocking, super-strong stone. Crushed pebbles are the ideal choice.
- Beauty and Function: Decorative rocks, drainage fill – crushed pebbles work well and look good.
- Big Digs: Big projects near gravel sources often use crushed pebble directly for foundations, fill, or drainage, using its local supply and natural toughness.
Grinding Out the Gains: Optimizing Your Pebble Crushing Circuit
Throwing a crusher at the problem isn’t enough. Here’s how to squeeze every ounce of value from your cobble crushing operation, learned from hard-won field experience:
1. Crusher Choice: The Foundation
Get this wrong, and you’ll face constant headaches. The crusher type (almost always a tough cone crusher!) and size must perfectly match your tonnage, feed size, and desired product size. Choosing one too small is a major mistake. A slightly oversized crusher running comfortably is far better than a smaller one constantly overloaded and wearing out too fast. Don’t just buy a model number; understand what it can handle in your specific setup. Hydraulic tramp release? Essential insurance.
2. Liner Life = Profit Margin
This is where your big costs hide. Don’t buy cheap liners. Invest in top-quality, application-specific manganese steel or alloy liners. Watch wear like a hawk. Use laser profilers, keep detailed logs. Optimize the crushing chamber profile – a “finer” chamber gives different product than a “coarser” one. Match it to your goal. Modern crushers offer profiles; use this flexibility! Replacing liners before they catastrophically fail saves downtime costs that far outweigh the liner price itself.
3. Feed It Like You Mean It (Choke Feeding)
For cone crushers crushing pebbles, choke feeding is non-negotiable. Keep that crushing chamber full. This promotes vital inter-particle crushing (rock-on-rock action), improves product shape consistency, maximizes throughput, and extends liner life. Starving a cone crusher feeding pebbles is asking for trouble – poor shape, faster wear, machine instability. Your feeders and conveyors absolutely must be up to the job.
4. Know Your Enemy (Feed Size Control)
That scalping screen isn’t there for show. Make sure it works! Feeding oversized pebbles drastically cuts crusher capacity, causes power surges, and beats up your liners. Strictly respect the crusher’s maximum feed size limit. Know the size distribution of your incoming feed and adjust your scalping accordingly.
5. CSS: The Constant Tweak
The Closed-Side Setting (CSS) determines your product size. As liners wear, the CSS effectively gets larger, making the product coarser. Regularly check and adjust the CSS to keep hitting your target product size. Hydraulic adjustment makes this quick; manual adjustment is a pain but still essential. Ignore this, and your downstream process will suffer.
6. Listen to the Machine (Power & Automation)
The crusher’s power draw (amperage) directly shows its load. Use this signal! Modern automation systems can link power draw, feed rate, and CSS together, constantly fine-tuning performance for max efficiency and consistent product. This isn’t just fancy tech; it’s real-time cost protection.
7. Maintenance: Non-Negotiable Discipline
This is tough, dirty work. Strictly sticking to the preventative maintenance schedule is critical. Proper lubrication (right oil, clean oil, changed on time) for crusher bearings is its lifeline. Screen inspections, conveyor roller checks, dust suppression nozzle cleaning – it all matters. Waiting for breakdowns on a pebble circuit is a fast track to blown budgets and production nightmares. Schedule the maintenance time. The crusher doesn’t take breaks; its care can’t stop either.
The Bottom Line: Why Crushing Pebbles Crushes Your Costs
Getting pebble crushing right isn’t just operational; it’s financial alchemy:
- More Product Out the Gate: Especially crucial for mills. Clear that SAG mill jam and watch your whole plant process more tons (and profits go up). This is the biggest, fastest win.
- Slashing the Power Bill: Taking hard pebbles out of the SAG mill lets it run smoother, grinding softer rock faster. Huge energy savings per ton of final product. Crushing pebbles directly uses way less power than grinding them in the mill.
- Smoother Sailing: Steady grinding means fewer quick fixes by operators, fewer breakdowns or hiccups, and reliable, uniform quality. Fewer surprises saves money and headaches.
- Lower Cost Per Ton: Fewer liner replacements, less power used per ton crushed, less breakdown downtime – it all cuts your running costs. Top-quality liners often pay off fast.
- Aggregate You Can Bank On: Tight control gives you uniformly shaped, perfectly sized gravel that sells for more and hits all the specs. Top quality builds your name.
- Turning Waste into Wealth: That pesky recirculating load? It’s valuable ore getting processed. That river rock pile? It’s high-grade gravel getting sold. Smart crushing turns waste into cash.
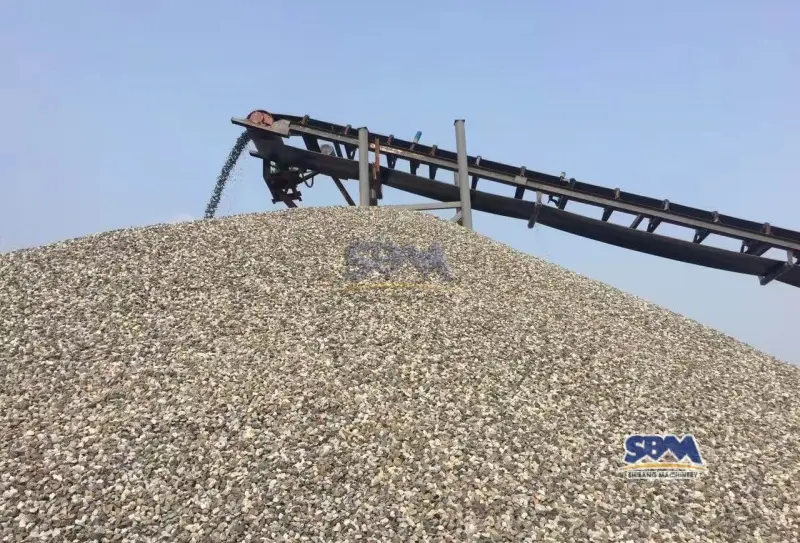
Picking Your Pit Partner: It Matters
As manufacturers, we live and breathe this stuff. Your crushing operation is critical path. Choosing the right pebble crushing equipment and, crucially, the right partner, makes all the difference. Look beyond the brochure:
- Technology That’s Battle-Tested: Does the equipment have a proven track record in abrasive, high-impact applications like yours? Ask for references in your sector.
- Application Experts, Not Just Salespeople: Do they understand the unique headaches of SAG mill recirculation? The specific demands of producing railroad ballast from river gravel? They need to speak your language.
- Built for the Long Haul: Inspect the build quality. Thicker steel? Robust bearings? Thoughtful access for maintenance? This machine will be punished; it needs to be tough.
- Control That Empowers: Can operators easily monitor and adjust? Does it offer automation potential? Good control prevents problems and maximizes yield.
- Support You Can Actually Rely On: Global parts availability matters when you’re down. Technical service teams who’ve seen it all? Priceless. Look for partners invested in your uptime. (Considering SBM China’s solutions? We see their heavy-duty cone crushers like the HPT series frequently spec’d for tough pebble duty, often praised for robust construction and hydraulic control. Their global support footprint is also a key factor for many international miners and aggregate producers. Worth a look for your specific needs – https://www.mill-sbm.com).
From Headache to Advantage
So, what is pebble crushing? It’s the vital, hands-on job of handling nature’s toughest small rocks to keep your plant running and making money. It’s not fancy, but it’s absolutely key. It needs tough, purpose-built gear – mainly cone crushers built super strong – and solid, careful operation. By getting the challenge, choosing machines made to last, and sticking to the best ways to manage feeding, liners, and upkeep, you turn pebbles from a costly problem into a booster for efficiency and profit. Whether it’s freeing up your SAG mill or making top-quality aggregate, getting good at pebble crushing is central to doing well. Those smooth, hard stones? They’re not just problems; they’re chances waiting to be tapped. Go get ‘em.
Headquaters Office
Whatsapp:+8615225176731
Email: [email protected]
Address: No. 1688, Gaoke East Road, Pudong new district, Shanghai, China.
Website: https://www.mill-sbm.com/