Email: [email protected]
The process of steel ore processing
What is the processing of iron ore? Imagine the atmosphere at the mines that morning. A thin fog has just been parted, cold air piercing bones. In front of us, chunks of raw iron ore results of the previous night blasting, big, hard, and dusty. They look like ordinary stones, useless. But for those of us who are involved in this industry, Every lump is the beginning of a long adventure. A complicated and amazing journey to turn raw materials into steel that builds the world. The process of steel ore processing This is not just a business and chemical business; This is about accuracy, experience, and a little touch of art. Let's explore together, As I often explain to the team in the field.

Recognize “Si the country” from inside the earth: What is iron ore?
Before we discuss the process of steel ore processing, we need to know well with “the character”. Bijih besi it's not a pure iron ready to use. He is more like a rock that stores an iron treasure in it, mixed with various other minerals (gang). The main types have different properties, And this is very important to determine the strategy Iron mineral processing Later. From experience, wrong identification of ore in the beginning can be expensive in the next stage!
- Hematit (Fe₂O₃): We encounter this brownish red. The iron content is decent, around 50-65%. The appearance is sometimes deceptive, but he's the most so “main raw materials” In many factories.
- Magnet (Fe₃O₄): Nah, This is a favorite of many operators! The color is jet black, and the most special, He is interested in magnets. The iron content can reach 60-70% even more! Efisiensinya biaa lebih tinggi dalam pemisahan. If you find a good magnetite deposit, raa kayak ketemu harta karun!
- Goethite/Limonite (FeO(OH)Nh₂o): The iron ore that contains this water. The iron content is lower, and often more “fussy” In processing. But still important, especially in certain sources.
- Siderite (Feco₃): The carbonate. Need special treatment such as roasting before further processing. Not too common, but still need to watch out for.
Understanding the character of each type of ore is like knowing the enemy (or a friend) Before fighting. This is the foundation for designingthe flow of iron ore production efficient and minimal problems.
Level 1: Ore preparation – “Disassemble” Big stone so small
The first stepthe process of steel ore processing This might sound simple: Breaking down large chunks into small pieces. But make no mistake, This is crucial! Imagine a new ore out of the fare, the size can be as big as a small car! The goal is clear: freeing valuable iron mineral grains from side stones (gang) who surrounded it, while making the size suitable for the next separation process.
Destruction (Crushing): This is our part!
- Primary destruction: This is where heavy machines like Jaw Curser play. This machine is like a giant that has an iron jaw. His job? Receive a large chunks and solve it into a fraction of the size 150-250 mm. I remember right, first in the Kalimantan project, one unit Jaw Curser we (like seri PE) have to work extra hard to deal with very abrasive ore. Reliability at this stage determines everything. The sound of the engine is the threat and the vibration that is felt to the bone is “music” which indicates running production. If this machine is sulking, The entire factory can stop!
- Secondary destruction & Tertiary: After being on”bother” by Jaw Crusher, Material enters to a further level of refinement with Cone Crusher or Impact Crusher. The target? Get a smaller size, biaa di bawah 25mm. For hard and abrasive iron ore, Cone Crusher often the first choice because it is more resistant to wear. Our bitter experience has occurred when forcing an impact crusher for super hard magnetite ore - the cost of replacing parts of the ASus parts! The right tool selection here is not just a matter of machine prices, but more to long -term operational costs. Energy efficiency is also much better if the tool matches the character of ore.
Milling (Grinding): Towards extreme fineness
If crushing already made the ore “Quite small”, Grinding made it Very smooth, Even like flour (Often smaller than 0.1mm!). The main tool is Ball Mill or Rod Mill. Imagine a large drum spinning, inside it is filled with steel balls or steel rods. Material entered, and when the drum rotates, The balls hit each other and crushed the ore until smooth. This process is very wasteful of energy! But this is the price to be paid to free as many iron mineral grains as possible. The roar of the ball mill that operates 24/7 it's like a factory heartbeat. If suddenly silent, There must be a serious problem.
Table: The need for particle size for different separation methods – Lessons from the field
Separation method | Ideal particle size | Practical Notes & Our experience |
---|---|---|
Magnetic separation | Relatively rough (1mm – 0.15mm) | Most efficient for magnetite. Larger size makes it easy to separate and reduce the risk of loss of fine minerals. If it's too smooth, can escape without being interested! |
Flotation | Very smooth (<0.15mm, even <0.045mm) | Need a wide surface. Getting smoother, The better for “stick” to the air bubble. But be careful, ores that are too fine can also increase chemical reagent consumption and waste treatment costs (tailing). |
Separation of gravity | Varies (5mm – 0.075mm) | Depending on the tool (Jig, Spiral, dll). Difference in specific gravity (density) must be clear. For iron ore, This method is often used as an initial stage (pre-concentration) before entering magnetic or flotation, especially if there are other heavy minerals that are beneficial. |
Level 2: Concentration – “Separate wheat from husk”
This is the essence ofthe process of steel ore processing: separates the valuable iron mineral from impurities (gang) which is useless. The technique is different, depending on the nature of the ore. This is a part that is often full of surprises!
Magnetic separation (Magnetic Separation): Very effective for magnetite!
Ini biaa jadi andalan utama kalau bijihnya magnetit. The principle is simple but sophisticated: Material that has been smooth is flowed above or near a strong magnet (can be permanent or electromagnetic magnet). Magnetite particles that are attracted to magnets will stick or turn the pathway, separate from the non-magnetic gangue. The magnetic power is crucial, biaa di kisaran 5000-6000 Gauss or more. I was always amazed to see the black particle suddenly “fly” towards magnets, Like there is magic. The efficiency of this method is high, and the operating costs are relatively lower than flotation. But yes, only effective for minerals that are magnetic such as magnetite.
Flotation (Flotation): The art of floating minerals
For hematite or ore that is not magnetic, Flotation is often an option. This chemical-physical process is quite complicated. Fine ore mixed with water and added special chemical reagents (Collector, frother, dll). This collector reagent makes the surface of the iron particle become “afraid of water” (hydrophobic). So, Air is blown into a mixture, Creating small bubbles. Iron particles that have been hydrophobic will stick to the air bubbles and lifted to the surface to form the . This is then dredged as a concentrate. Temporary, impurities “love to water” (hydrophilic) will sink. This process is like magic! But it takes strict supervision. Wrong a little dose of reagent, or pH of non -pass water, The results can be chaotic. Experience in the field teaches, The experienced flotation operator is very valuable!
Separation of gravity (Gravity Separation): Take advantage of weight differences
This technique utilizes differences in specific gravity (density) between iron minerals (biaa lebih berat) and Gangue (biaa lebih ringan). Tools like Jig or Spiral Concentrator used. In water media, heavier particles will sink faster or move to different paths than light particles. This is a relatively simpler method and low costs, and environmentally friendly because of minimal chemicals. Often used as an initial stage to reduce the burden of the next process (pre-concentration), or for certain types of ore where the difference in specific gravity is very striking. Seeing heavy mineral particles separately by itself because gravity always makes me remember how natural laws work elegantly.
The result of a successful concentration stage is Iron ore concentrate. This fine powder whose iron content is much higher (Can 60-68% Fe for magnetite, or 58-64% for hematite) compared to raw ore. Imagine, The material mass that must be transported and processed can then be reduced dramatically because the gangue is discarded! This is a significant logistics and energy savings in processing process iron.
Level 3: Agglomeration – “Re -form the fine powder”
The iron ore concentrate is very fine powder. If put just like that into the blast furnace (stove), The result will be messy! The fine powder will clog the gas flow, The reaction is uneven, and efficiency drops dramatically. So, Iron ore processing stages Next is dilating, aka re -forming the powder into a larger lump, strong, and porous.
1. Pellet making (Pelletizing): Make “Marbles” Iron
This is a sufficient process “aesthetic”. Fine concentrate mixed with a binder (biaa bentonit, a kind of clay) and a little water. This wet mixture is then put into a named tool pelletizing disc (Rotating disk) or pelletizing drum (drums spinning). This rotating movement makes the mixture roll up and form small balls like marbles, biaa berdiameter 9-16 mm. This wet pellet is still fragile. So, They must be dried first, then put in a very high temperature stove (around 1300 ° C.) for the process induration (hardening). At this high temperature, Syinter reactions occur between particles, make a pellet hard, strong, and porous. Pellets produced uniformly, easy to handle, and becomes the main raw material that is very efficient for modern blast furnaces. The process of making a good pellet needs precision; water rate, Turn speed, and induration temperature must be right. If not, Pellets can crush on the trip or in the furnace.
2. Sintering: Alternative for fine particles and dust
Another common method is syntering. This is mainly used to process very fine ore particles, factory dust, or concentrate that is not suitable for pellets. A mixture of fine material (can include concentrate, small -sized ore, lime/dolomite as flux, and cokeze/coke powder as fuel) arranged above a “pallet” move. This mixture is then passed through the burning zone (ignition hood) where the surface is turned on. Fire later “spread” down through the material layer, assisted by air gusts from below. The temperature reaches around 1200-1300 ° C (under the melting point of iron). At this temperature, The surface of the particle melts slightly and blends (sinter) forming a porous lump called a sinter cake. After cold, This sinter cake is destroyed and filtered into a size that is suitable for blast furnaces (biaa 5-50mm).
Sinter is not as fast as pellets and the shape is less uniform, but it remains an important ingredient of blast furnace filling, especially for re -processing fine waste. The distinctive smell of the sytering process is difficult to forget for anyone who has worked in an iron factory!
Both pellets and sinters have advantages: Uniform size (relatively), strong so that it is not destroyed when stacked or put into the furnace, and most importantly, porous. This porosity allows gas reductors (from below) flow smoothly to all parts of the stove, so that the reduction reaction can occur efficiently and evenly. Choosing between investing in pellet factory or cyter factory is often a company's strategic decision, Based on the main type of ore, investment costs, and availability of additional raw materials.
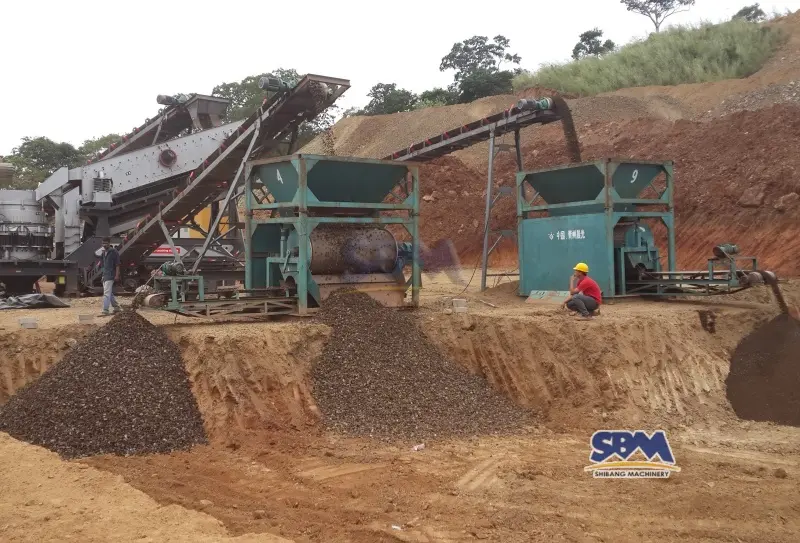
Level 4: Reduction – “Take the oxygen, Be a metal”
This is the real heart ofthe process of steel ore processing: changed the iron ore (especially iron oxide) becomes an iron metal by taking its oxygen. This reduction process is the core of everything. There are two main paths that develop in the industry:
Blast Furnace (Stove): The traditional giant
This is still the most global dominant method. Imagine a giant tower (blast furnace) which can be tens of meters high. From above, inserted layered: bait (can pellets, sinter, or sometimes a certain size ore), cooked (Coal that has been processed, functions as fuel as well as a source of carbon for reduction), and flux (limestone/dolomite, to bind impurities). From the bottom, blown hot air (can reach 1200 ° C.) that oxygen enriched. In this hot stove, a series of complex chemical reactions occurred:
- Cooked (C) react with oxygen (O₂) form carbon monoxide (CO).
C + O₂ -> CO₂
, ThenCO₂ + C -> 2CO
- This hot CO gas rises to the top through the material layer.
- Co react with iron ore (misal hematit, Fe₂O₃), take the oxygen and reduce it into metal liquid iron (Fe).
3CO + Fe₂O₃ -> 2Fe + 3CO₂
(Simply put). - Flux (kapur) react with the main impurities in ore (Like Silika Sio₂ and Alumina Al₂o₃) forming a liquid terp (slag) lighter.
CaO + SiO₂ -> CaSiO₃
(sweat). - Melted iron (which are called pig iron or coarse iron, contains high carbon ~ 4% and other impurities such as SI, Mn, P) collected at the bottom of the stove.
- Hit, Because it is lighter, float over liquid iron.
- Periodically, Liquid iron and liquid slag is removed from the furnace through the tap hole (tapping hole) different. The atmosphere around Blast Furnace when tapping was spectacular (and it's so hot!) -spray fire and liquid metal. Pig iron This is the basic material for making steel. Working near Blast Furnace teaches the meaning of the word “intensity” the indeed.
Direct Reduced Iron (DRI) / Sponge Iron: Alternative paths that develop
Along with the environmental demands and the availability of fuel, the drip strip (Direct reduction iron) All Chonen Iron (Iron sponge) more popular, especially in areas with abundant natural gas supply or who want to reduce carbon traces. This process does not melt ore. Reducing gas (especially hydrogen h₂ and carbon monoxide co), produced from natural gas (reforming), flowed into the reactor (shaft furnace, rotary kiln, fluidized bed) that contains steel ore pellets or mud ore (lump ore) high quality. At high temperatures (biaa 800-1050°C, under the melting point of iron), This reducing gas reacts directly with iron ore, take the oxygen. Fe₂O₃ + 3H₂ -> 2Fe + 3H₂O
or Fe₂O₃ + 3CO -> 2Fe + 3CO₂
.
The result is porous solid iron (like a sponge, so called iron sponges) With very high iron content (90-94% Fe) and low impurities content. This product is called dri (Direct Reduced Iron) Or if compacted further into hot briquettes, called HBI (Hot Briquetted Iron). DRI/HBI is mainly used as premium raw material in Electric Arc Furnace (EAF) For steel making. The advantages of the DRI path are co₂ emissions which are in theory lower (especially if using H₂ green), And the scale can be more flexible than giant blast furnaces. This is a very dynamic and promising area for the future Iron mineral processing the greener.
Level 5: Steel making – “Perfect the metal”
Pig iron from blast furnace or dri from the direct reduction factory, even though it is in the form of iron, not suitable for most applications. The carbon content is still high (4% on pig iron), And there are various impurities such as silicon, Mangan, Phosphorus, and sulfur. Process iron ore processing Continuing by perfecting this metal into steel, namely a combination of iron with controlled carbon content (biaa di bawah 2%) and minimized impurities.
1. Basic Oxygen Furnace (BOF): Fast and Efficient
This method is the most commonly used in the world, especially using pig iron liquid as the main raw material (biaa >70-80%), plus scrap metal (scrap) and a little flux. The process is fast and intensive! Pig iron liquid poured into the BOF converter (a large container shaped pear). So, A Lance (pipa) lowered and exhaled pure oxygen (99%+) with very high speed to the surface of the liquid metal. This oxygen reacts very exothermic (produce heat) with carbon and impurities in pig iron.
- Carbon (C) Burned into CO/CO₂ gas.
- Silicone (And), Mangan (Mn), Phosphorus (P) also oxidized.
- Kapur (CaO) which added to react with impurities oxides (especially sio₂ and p₂o₅) form a lot of slag.
This process only takes about 15-25 minutes per “charge”! The temperature can reach 1700 ° C. By controlling the amount of oxygen and time, steel composition can be arranged very precisely. After sampling and quick analysis ensures the right composition, liquid fertilizer then poured into a ladle (pouring pan) for the next pouring process. The speed of this Bof is really amazing to watch it.
2. Electric Arc Furnace (EAF): The flexible electric fueled
Electric Arc Furnace (EAF) more popular, especially in “mini-mills”. This process relies on scrap metal (scrap >90%) or a mixture of scrap and DRI/HBI as the main raw material. The heat source comes from high voltage electricity which is flowed through Giant graphite electrode on a bowl -shaped furnace.
Electric arc between electrodes and raw materials produces extreme heat (>3000°C) which melts the material quickly. The completion of liquid fertilizers involves:
- Oxygen shooting: Burning impurities & regulate carbon.
- Addition of charcoal powder: Adjust the carbon rate.
- The addition of flux (kapur): Forming a slag of impurities.
EAF advantages:
- Flexible: Easy Start/Stop Operation.
- Recycled based: Dominant scrap metal.
- Co₂ lower emissions: Especially with renewable energy.
- Special voice: The electric buzzing of the electric arc is intense (need ear protector).
Final product EAF or BOF ismelted Specific composition (example: low carbon steel). This steel is then processed onContinuous pouring machine (CCM) to freeze into:
- Slab (thick plates for plates/pipes)
- Bloom (Large box for structural profiles)
- Billet (Small/round boxes for stems/wires)
This semi -finished product is then processed through bokering or withdrawal to the final steel product. (hot rolling), cold roll (cold rolling), withdrawal (drawing), or other processes into a variety of final steel products that we know: ship plate, pipeline, concrete stem (rebar), wire, automotive sheet, Building Profile, and still a lot more. Processing process iron The long and complex finally empties into the products that form the infrastructure of our lives.
Back to the beginning: Why is the selection of the destroyer so crucial?
As a person who deals with a crusher and a processing factory every day, I can't emphasize how important the strong foundation is.The process of steel ore processing starting from effective destruction. If this level is problematic, The eternal effect will be felt to the end of the process.
- Jaw Curser: This is the front guard. He must be tough, reliable, and able to withstand shock (impact) from the large chunks that come in. Experience on the field teaches that the power of frames, Jaw steel quality (jaw plate), and a simple adjustment system is a key. Like a unit PE Series We are designed for heavy loads and hard mining conditions. If Jaw Crusher is often jammed or quickly worn out, The entire factory rhythm will be chaotic. Investment in a good jaw crusher is like buying a strong house foundation.
- Cone Crusher: After being on”bother” by Jaw Crusher, Cone Crusher is tasked with producing a final product that is smooth and good. For abrasive iron ore, wear resistance is everything. Mantel (mantle) and concave (concave) must be made of high -lasting manganese steel. The efficiency of destruction is also vital to save energy. A cone crusher which works optimally will produce products with a consistent size distribution, which is very important for the performance of the ball mill and the next concentration process. The wrong selection of cone crusher can make the cost of replacing the wear parts swell and the energy consumption is soaring. Iron mineral processing which is efficient starting from here.
Choosing a machine is not just a matter of specifications on paper. This is about understanding the character of local ore, capacity needed, and reliable after -sales support. We often see customers who were initially tempted by cheap engine prices, But eventually cost more for repairs and downtime. Reliability is everything in guardingthe flow of iron ore production keep flowing smoothly and profitable.
Cover: An amazing long journey
So, What is the processing of iron ore? This is an epic industrial saga. From lumps of hard and non -shaped stones at the bottom of the mine, through a series of complex physical and chemical transformations, until finally it became a strong steel that forms the backbone of modern civilization. Every stage - destruction, milling, separation, agglomeration, reduction, Purification - Requires in -depth knowledge, Sophisticated technology, and reliable equipment.
UnderstandIron ore processing stages as a whole is not just a business engineer or factory manager. This is the key to making smart investment decisions, Optimizing operational efficiency that has an impact on production costs, minimize environmental impacts, and in the end, ensure business sustainability. Of sbm china, be part of this trip by providing a destroyer that is the backbone of the early stages of the process, is an honor and pride. We witnessed firsthand how reliable and efficient machines could be a catalyst for operating successIron mineral processing our customers.
If you are planning a new factory, expand capacity, or just want to optimize the performance of existing destroyers, Don't hesitate to discuss with us. Our experienced technical team is ready to listen to your specific challenges and recommend the best solutions supported by the latest technology and full service commitment. Let's jointly build a stronger mineral processing industry, efficient, and ongoing!
FAQ: Answers to field experience
1. What are the intermediate products and the main end of this processing chain?
- Antara Product: Iron ore concentrate (fine iron powder), Pellet, Sinter, Pig iron (Pig Iron – liquid/compact), Iron sponge (DRI/HBI – congested).
- Main final product: Steel in various forms (Slab, Bloom, Billet, Plate, Trunk/wire rebar, Pipa, Structural profile, Thin sheet, dll).
2. Why can't I immediately put a fine concentrate into the blast furnace?
- Gas flow blockage: Fine powder will solidify and clog the space between the material, block the flow of gas reductors (CO) from the bottom up. Reduction efficiency drops dramatically.
- Fluidization: Pressurized gas can cause fine powder to behave like fluid (Fluidated), make operations unstable and dangerous.
- Uneven heat distribution: The reaction does not occur homogeneously.
- Loss of material: Fine powder easily carried by the gas out of the chimney (dust loss). Pellets/Sinters solve all these problems with uniform sizes, strength, and its porosity.
3. What are the advantages and disadvantages of blast furnace (BF) vs Direct Reduction (DR)?
- Blast Furnace (BF):
- Advantage: Very large capacity (economical scale), mature technology, can use various bait (pellet, sinter, lump ore), pig iron liquid directly to the BOF.
- Deficit: Investment is very large, high dependence on coke (mahal, high emissions), Co₂ emissions are very significant, Continuous process is difficult to stop.
- Direct Reduction (DR):
- Advantage: No need to coke (Use natural gas/hydrogen), CO₂ emission potential lower (Especially with H₂ Green), smaller investment (a more flexible scale), DRI/HBI products are low (Premium for EAF).
- Deficit: Requires high quality ore/pellets (High Fe, low impurities), Dependence on Natural Gas/Reductor, solid product (need to be led again in EAF), the capacity is generally smaller than a giant BF.
4. Whether one type of crusher can handle all types of iron ore?
Very not recommended! Iron ore has different characteristics:
- Violence (Hardness): The ore is very hard (For example hard magnetite) need a crusher with a strong compression style like Jaw and Cone Crusher. Impact Crusher may be fast worn.
- Abrasivitas (Abrasiveness): Abrasive ore requires a wear part (Like Jaw Plate, mantle, concave) from the material is very resistant to wear (high manganese steel). The design of the crusher room is also influential.
- The contents of the clay (Moisture & Clay): Wet ore or containing clay can clog certain crusher. Sometimes you need a special pre-screening or feeder.
- Bait size & Products needed: Determine the type of crusher (primer, seconds, tertiary) and configuration. The right selection has a major impact on operating costs and the final results. Consultation with experts and trials in the lab/pilot plant is very important.
5. What is the most difficult challenge that is often faced in iron ore processing plant?
- Fluctuations of ore quality: Ore from one mine can change the quality, Forcing the process of continuous process. Need a responsive control system.
- High energy costs: The grinding level (grinding) and blast furnace is very wasteful of energy. Energy efficiency is the main focus.
- Waste management: Volume tailing (Waste from concentration) Then battle (sweat) very large. Handling, storage, and re -utilization (If possible) is an environmental challenge and cost.
- Environmental impact: CO₂ emission (especially from BF), particle emissions, water use, and land disturbance.
- Maintenance costs & Machine availability: The engine in the abrasive and corrosive environment quickly worn out. Downtime for treatment must be minimized. The reliability of the crucial crushing machine.
- Price fluctuations: The price of iron ore and steel is very fluctuating, affect profitability.
6. The direction of the development of iron ore processing technology going forward?
- Decarbonization: This is the hottest! Focus on:
- DR Green Hydrogen Based (H₂-DRI): Replace natural gas with H₂ produced from water electrolysis using renewable energy. Target zero carbon emissions in the reduction process.
- Green Electric Based Eaf Smelting: Use electricity from renewable sources for eAF that uses dri/HBI and scrap.
- CCUS (Carbon Capture, Utilization, and Storage): Capture co₂ from BF/BOF exhaust gas and store it or use it.
- Use of waste: Increase the use of slag as building materials (Aggregate substitute, semen) and valuable mineral recovery from tailings.
- Digitalization & Automation: Utilization of AI, IoT, and big data for optimization of real-time processes, Machine maintenance predictions (predictive maintenance), improvement and efficiency. Sensors on the crusher and conveyor can monitor vibrations, temperature, burden to detect early problems.
- More energy efficient process: The development of more energy -efficient grinding technology, more efficient alternative reduction process, and optimization of the use of exhaust heat.
- A reduction of water consumption: Closed water circulation (close loop) In the process, the better Dewatering Tailing technology.
Headquaters Office
Whatsapp:+8615225176731
Email: [email protected]
Address: No. 1688, Gaoke East Road, Pudong new district, Shanghai, China.
Website: https://www.mill-sbm.com/